Lean Manufacturing & ERP: Why Lean neednt stop on the shop floor
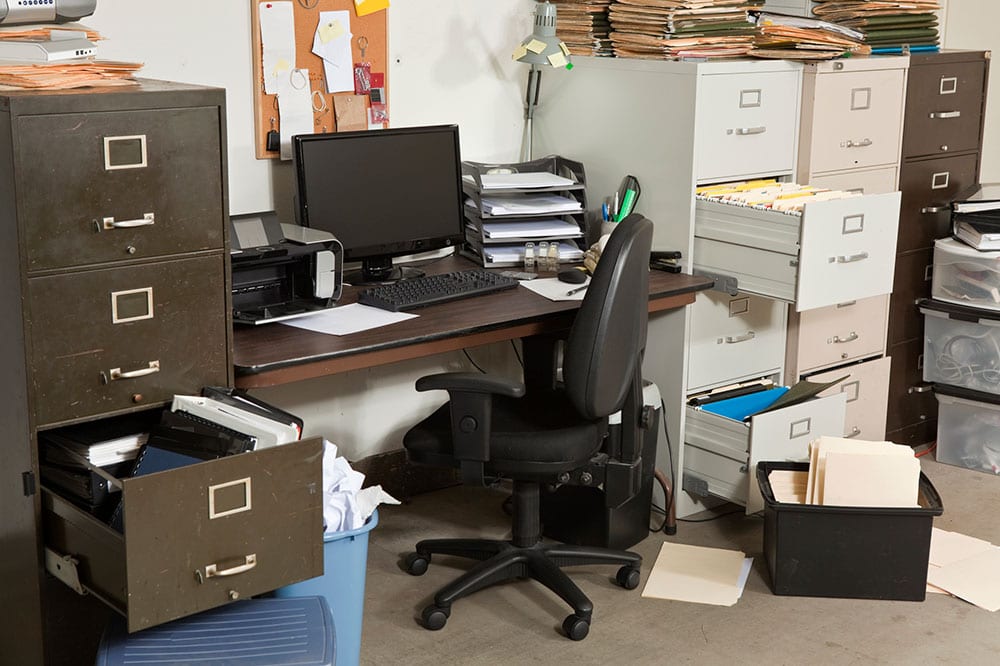
We were saddened to see increasing numbers of manufacturers and engineering companies suspending operations during the COVID-19 crisis due to the difficulty of keeping their teams safe, the challenges of obtaining raw materials and lack of demand from customers. Whilst there are very few positives about this situation, this downtime gave us all extra time to consider future business strategies and approaches. We can say with confidence that we won’t be going back to life as it was at the start of 2020 – things will be very different in the post-virus landscape. Looking now at your business and identifying areas of waste in terms of efficiencies, time, resources and processes will help your company get back up to speed much more quickly.
Lean Manufacturing
Using the Lean approach is a popular choice amongst many of our customers and other organisations in manufacturing. In Lean methodology you focus on creating more value-add for customers with fewer resources. By adopting the 5 key principles (see below), manufacturers can identify and cease activities that use resources but don’t add any value.
Using ERP in Lean Manufacturing
ERP is a tool that helps you achieve a Lean way of operating. An ERP system gives you visibility of everything happening in your business and enables you to understand what your customers want, based on data stored in the ERP, including previous sales orders, trends and other data.
You can reduce your inventory, improve cashflow and cut costs because it’s so much easier to match your output to customer demand with an ERP system.
And with a system like E-Max ERP, you can also reduce manual work and automate business processes. These processes are continually reviewed and streamlined, to keep you on the most efficient path.
But ERP doesn’t just help you control your shop floor, improve quality and manage inventory. Administration or office processes can account for over 30% of a manufacturer’s costs. A significant amount of lead time in manufacturing (we’ve read possibly as much as 80%) is due to administrative or office processes. Lean principles can be applied to these areas but in our experience (and by the admission of many companies we speak to) rarely are. Imagine what time and cost savings you could be making if you could adopt Lean in the office too…..
Lean needn’t (and shouldn’t!) stop at the office door
So how can Lean manufacturing and ERP break through your office door?
1. Standardise your admin processes with ERP
All your processes are mapped out and the same steps applied by every member of your team, ensuring consistency, minimising errors and providing visibility of everyone’s activities. Have you ever wondered whether your sales team are following up every lead religiously? Now you know!
2. Improve work standards and reduce mistakes
Mistakes do happen but it’s frustrating when your production is brought to a standstill because someone in the office forgot to tick a box on a form somewhere. An ERP system automates all your company documents, and settings applied to each field. Activities can’t progress until every necessary field is completed, accurately. Hooray for automated quality control!
3. Minimise duplication and waste
Eliminating waste is a fundamental principle behind Lean. Every time one of your employees performs an activity already done by someone else is a drain on your resource and a cost implication.
Think of customer emails that are forwarded multiple times through different departments (an enquiry for a job received by Sales, then forwarded to Estimating, then forwarded on to Production to check lead times, and on it goes.)
Then there’s the spreadsheets that are passed around to confirm the BOM is correct before going to Purchasing and being added to the purchasing spreadsheet so a PO can be arranged. And what about printouts of documents that need multiple revisions?
By storing everything centrally (in an ERP) the right people can access the right information whenever they need it.
4. Practice continuous improvement
Another fundamental principle of Lean is the concept of continuous improvement. How many times have you heard the objection “But we’ve always done it like this!” An ERP (such as E-Max ERP) gives you visibility of your now standardised processes (via our dynamic dashboard). With a tool like this, you can identify where logjams exist and take remedial action to smooth the flow of an administrative process.
How many times has your Purchasing team had to sit around waiting on the last price to come in from a particular supplier when all your other suppliers responded days ago? ERP software allows you to identify regular offenders and speed up your processes.
And there you have it. Lean manufacturing and ERP can work hand in hand to deliver efficiencies across every area of your business, eliminating waste and adding greater value to your customers. So don’t let Lean stop at your office door – give us a call now on 0808 109 2035, email us or arrange a short personalised online demo to see what else E-Max ERP can do for your business.