Production Control & Scheduling
Effective planning and organisation of resources is a key element in a company’s operations. Our production control module is built upon our very successful tried and tested original MRP system and continues to be the core of E-Max ERP. By providing all the functionality you need, our Production Control & MRP module will maximise your company’s efficiency and deliver a competitive advantage.
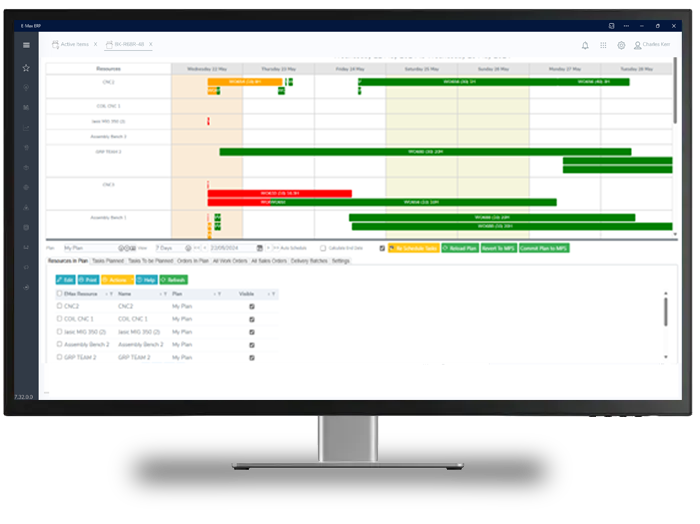
Take Control Of Your Production
By bringing your production planning and shop floor activity into one single system, you can optimise your production processes and resource allocation, creating previously unobtainable levels of operating efficiency.Real Time Visibility
E-Max ERP provides real time visibility into the shop floor activities, allowing you to monitor production performance and resource utilisation, and spot process bottlenecks. Identify late-running jobs and issues as they happen and make informed strategic decisions to rectify these.Bill of Materials (BOM)
E-Max’s bill of materials allows you to accurately define all the components, materials, parts, subassemblies and quantities required to manufacture a finished product. Starting with the finished product at the top, its hierarchical structure allows infinite multi-level BOMs of unlimited size. Save time by duplicating existing BOMs, use the tracking history to record revisions (ideal for audit purposes), and import BOMs from other software packages, including Excel and CAD packages. Included in E-Max ERP’s BOM is a standard item configurator.Multiple Unit of Measure (UOM) & Conversions
E-Max ERP gives you the ability to measure materials precisely, based on your preferences. Stay in control of various units of measurement for your inventory. Establish conversion ratios directly within the system, ensuring seamless management of sales, purchases, and stock transactions. The system will seamlessly manage all conversions on your behalf.Material Requirement Planning (MRP)
E-Max’s MRP functionality is at the core of our cloud ERP software and is built upon our very successful tried and tested original MRP system. Utilise E-Max ERP’s comprehensive MRP to plan and control the materials you need for production. Calculate the precise quantities of raw materials, components, and finished goods required to meet your production schedules and customer demand. E-Max’s MRP functionality ensures you have the right materials available at the right time, in the correct quantities, and at the right cost to support production processes while minimising inventory costs and reducing waste and production delays.Manage Your Resources Effectively
Take your MRP to the next level with E-Max ERP as you plan, monitor and organise your resources to meet customer deadlines. E-Max ERP allows you to schedule activities, taking into account availability of labour, including specific skill levels, machinery, tools, and workstations to create optimal production plans. In addition to daily, weekly, and monthly planning, our MRP functionality can be used for long term planning and forecasting.Shopfloor Management
Schedule and monitor your production activities on the shop floor. E-Max ERP tracks the progress of work orders, manages work-in-progress, and ensures that production processes are performed efficiently.Understand Your Production Costs
Get clear visibility over planned and actual production costs with E-Max ERP. Calculate labour costs and track set up times and run times, including cycle quantities and cycle time. Cycle times can be set as decimals of days, hours, minutes and even points of a second to allow precise and accurate costing. Track and cost any assembly work as it happens. Material costs are allocated to each job.Optimise Your Routing
Specify the tasks or operations and resources required for each job and the order in which these should be performed. With E-Max ERP you can create multiple route versions and add clear instructions and operator instructions on each route. Easily copy standard operations and routes from other parts. Store template routes and add different operations when required. Tests can also be assigned behind operations. Calculate planned labour costs and track set up times and run times, including cycle quantities and cycle time.Manage Efficiency
Factor in any time delays between operations and apply an efficiency percentage. Set routing constraints or dependencies to ensure tasks are performed in the correct order. Constraints can be Task to task; BOM to Task, BOM to BOM and can be added to specific routes or parts.Create Tasks Or Operations
Create a library of standard operations or tasks to quickly apply to a route. Assign key information to each operation including tooling costs and testing requirements. Resources can also be applied to operations with standard processes – apply skill levels to operations and ensure appropriate operators are allocated certain tasks or select individual resources and apply these when creating a route.Produce Job Packs
Connect the route cards, drawings and related documents, ie specifications, test results, safety information, specific instructions, for each job. E-Max includes functionality to locate and consolidate into one pack any required documents for a specific job, which can then all be printed at the touch of a button.Works Order Management
Generate works orders in a single click with E-Max ERP and keep your production moving. Guide your production team, coordinate your resources and ensure every job is manufactured to a quality standard and schedule. E-Max ERP supports multi-item works orders, allowing for nesting and by-products being returned to stock.Manage Scrap
Avoid material shortages and account for all material costs by recording scrap or wastage information. E-Max ERP allows you to apply a fixed quantity and/or percentage to all items, either purchased or manufactured, for accurate materials management. Fixed and percentage scrap is also handled at every level in our BOM.Live WIP tracking
Know the actual value of your work-in-progress at any point in time. As materials, time and subcontract costs are booked to jobs, your WIP value will be re-calculated to incorporate these in real time. As soon as the finished items are booked into stock, the value of these is transferred to inventory.Kitting and Material Issue
Whether you are releasing an individual item or raw material, or gathering and organising a number of components or parts for a specific assembly or production task, E-Max allows you to easily issue these from stock.Backflushing
If the exact quantities required for a job are not known, E-Max allows the materials or items used in that job to be removed from stock, using the pre-defined bill of materials (BOM), after production is completed or the finished item(s) receipted into stock.Item Revisions and Version Control
Achieve clear visibility and control of each different version of a BOM or route. As part of E-Max’s product lifecycle management, all revisions are tracked, with the current version being stored on the item or part master.Item Variants
With E-Max ERP you can store multiple manufacturing versions and routes for an item. Ideal for companies that offer customisable or configurable products to meet diverse customer needs. E-Max also offers ECN and change control options.Manage Subcontract Work
Get clear visibility of your subcontract costs and allocate these costs to the correct job.Integrated Quality System
E-Max ERP includes a robust quality system designed to monitor, control and improve the quality of production. Record non-conformances, identify root causes and make improvements. Find out more: link to actual quality page.Document Management
Use the flexibility of E-Max ERP to link any type of document against any transactions in E-Max, including sales orders, works orders, invoices, expenses, etc. Link critical documents like drawings, test results, procedures, images, instructions, and even chemical analysis to any job or operation and access every related document easily and quickly from anywhere within E-Max.Identify Late Orders Before They Occur
Get visibility across all your orders and their status. E-Max automatically calculates start dates based on required delivery dates to ensure you meet your customer requirements. Material issue dates are also calculated to provide the materials needed in time for the production phase, whilst alerts can be set to flag any late deliveries or other problems that may impact the job, such as machine unavailability. E-Max can also be used to understand the effects of scheduling in an emergency or ‘hot’ job and the downstream effects of this on other orders and inventory.Identify Your Available Capacity
Maximise your machine usage by understanding when your machines are running operations or not, allowing you to take on additional work without increasing capacity.Utilise Finite Scheduling
Set your parameters on each available resource in E-Max ERP to ensure no over-booking. The system’s scheduling engine creates a plan based on the most efficient delivery of jobs using all the information contained within E-Max ERP, including delivery dates and available resource. Our drag and drop functionality can also be used to fine tune planned schedules, for specific occasions when experience and knowledge come into play, ie consolidated set-ups.Multiple Traceability Options
Track items or raw materials throughout their journey through your production facility and onto delivery using one of E-Max ERP’s traceability options. These include Batch, Serial, First in First Out (FIFO), Last in First Out (LIFO) and Use by Date. Finished goods that are serialised can also be allocated serial numbers automatically.Factor in All Key Information to Improve Output
E-Max ERP includes individual schedules for each machine to ensure that both employee and machine downtime is minimised. Specialist skills of employees are also taken into account as are known bottlenecks in production. This improved planning and resource allocation also improves output levels.Calculate Weights of Finished Products
E-Max ERP calculates the finished weight of your manufactured products so these can be safely stored in your warehouse before being delivered to a customer or used in production of another product.Speeds & Feeds
Accurately calculate the time needed for machining operations, including turning, facing, grooving (diameter and face), drilling, tapping, and milling. Select the material the finished part is made from and E-Max ERP will use historical data on cutting speed and feed rates to calculate a predicted time for the activity.Ready to speed up your production?
Don't hesitate to contact us
E-Max ERP Software
With E-Max ERP you can easily manage