Traceability in Manufacturing
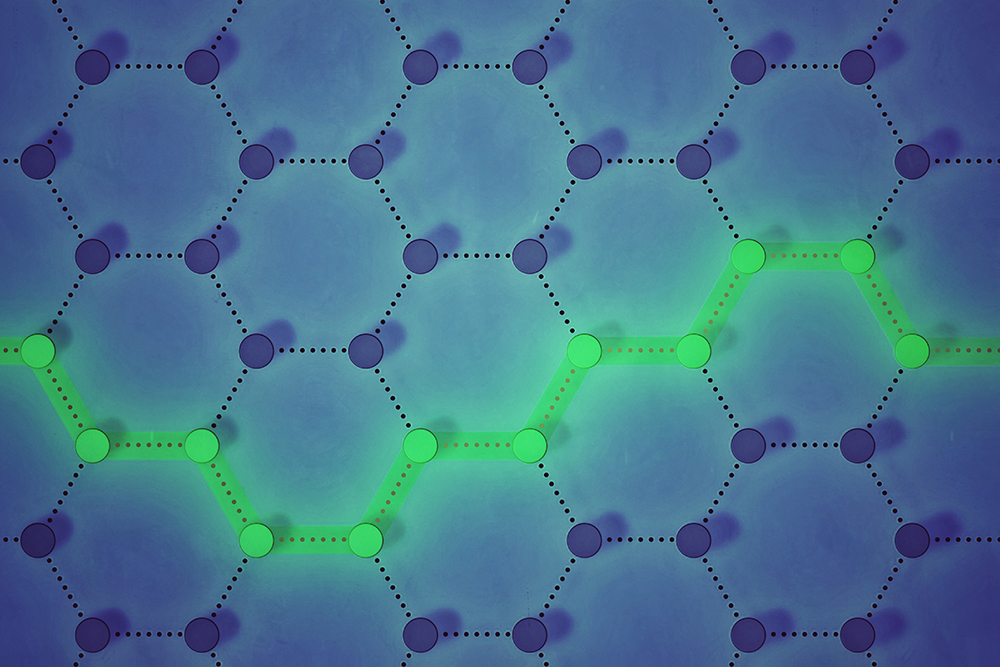
As the world becomes smaller and global supply chains more common, having full traceability in manufacturing is becoming ever more important to businesses. Many industries, including but not limited to, aerospace, defence, automotive, medical, food, and electronics, demand suppliers be able to account for the movement of materials throughout the entire manufacturing process to delivery. Manufacturers themselves also benefit in terms of cost, quality and reduced risk from implementing an effective manufacturing traceability system.
What is Manufacturing Traceability?
Manufacturing traceability is the ability to track every part of a product through the manufacturing process, from the moment raw materials are purchased to when the final product is shipped and beyond. Information is recorded at every stage of the process, tracking details such as who has worked on the product, what tools and machines have been used during production, and what quality checks were performed.
Why is Manufacturing Traceability so Important?
Aside from traceability being a basic requirement of many supplier contracts and often an industry regulation, there are plenty of other reasons manufacturers should be using a system to track and trace all parts going through their business. Chief amongst these are:
- Ability to respond quickly to problems. In the case of a product failure or recall, being able to identify every impacted batch or lot in real time is a necessity. A contained and controlled recall is much easier to manage and move on from.
- Analyse root causes. Is there the problem somewhere in the production process or perhaps the material sourced from a supplier is regularly substandard? Does a new employee require further training? Once identified, these issues can be worked on and resolved.
- Facilitate continuous improvement. By tracking parts and products through the manufacturing process, you can monitor and detect problem areas and bottlenecks. The data provided by a manufacturing traceability system should also be used to identify and correct previously undetected issues in the production process.
- Improve quality. Identifying points in the process where additional quality checks are required can result in early defect detection. The earlier a fault can be identified minimises the cost to the manufacturer.
- Reduce waste and costs associated with spoilage. Being able to identify and use material expiry dates allows these items to be scheduled into production earlier.
How to Manage Manufacturing Traceability
Managing traceability in manufacturing is not an easy task to do manually. The sheer volume of data that needs to be recorded, analysed and reported, even by a relatively small business, is best managed by a software application. Manufacturing ERP systems, such as E-Max ERP, are one of the most effective ways of managing traceability, with data flowing into them from all stages of the production process.
Most manufacturing ERP systems should include some traceability functionality but not all are as robust as E-Max ERP. Here’s some of what we offer:
- Serial number traceability
- Batch number traceability
- Manufacture date and expiry date tracking
- Supplier (and manufacturer if different) details for all incoming goods and materials
- Goods Received Notes (GNR) recorded in case of cross contamination
- Full tracking history of all movement of stock
- Composition of manufactured part, component or product – records the raw material used to make an item
- Distribution tracking after production
- Inventory management system integration including hardware like barcode scanners
- Any certificates and tests associated with raw material are logged to each production batch
- Logs changes to quality and quantity
- Traceability can commence from the point of raising the PO
- Extensive drill down on every point of data
E-Max ERP offers true bi-directional traceability meaning that if a supplier reports a flaw in raw material, it can be tracked through to the finished product and end customer. Likewise, if the customer reports a fault, that can be traced all the way back through the manufacturing process to the original raw materials.
RoHS and CoSHH
E-Max ERP also enables the tracking of hazardous substances as required by the Restriction of Hazardous Substances Directive (RoHS) and Control of Substances Hazardous to Health Regulations (CoSHH). Wherever hazardous materials are in use and/or when these are specific processes and procedures to be followed, E-Max highlights these to every relevant user. Through this unique functionality, a key requirement for electronics manufacturers in particular, full traceability is available on any hazardous material.
Manufacturing traceability will increasingly become a necessity for businesses going forward so they can remain compliant with industry regulations and meet customer requirements. A manufacturing ERP system, like E-Max ERP, means a transparent and accountable manufacturing process, leading to increased customer confidence and satisfaction with higher quality outputs.
If you’d like more information on E-Max ERP and our traceability functionality, take a look at our website, give us a call now on 0808 109 2035 or email us. We also be delighted to show you how it works in practice with a short personalised demo so you can see how your business can enjoy all the benefits a true manufacturing ERP system offers.