Using ERP for ISO 9001 Accreditation – make it easy on yourself
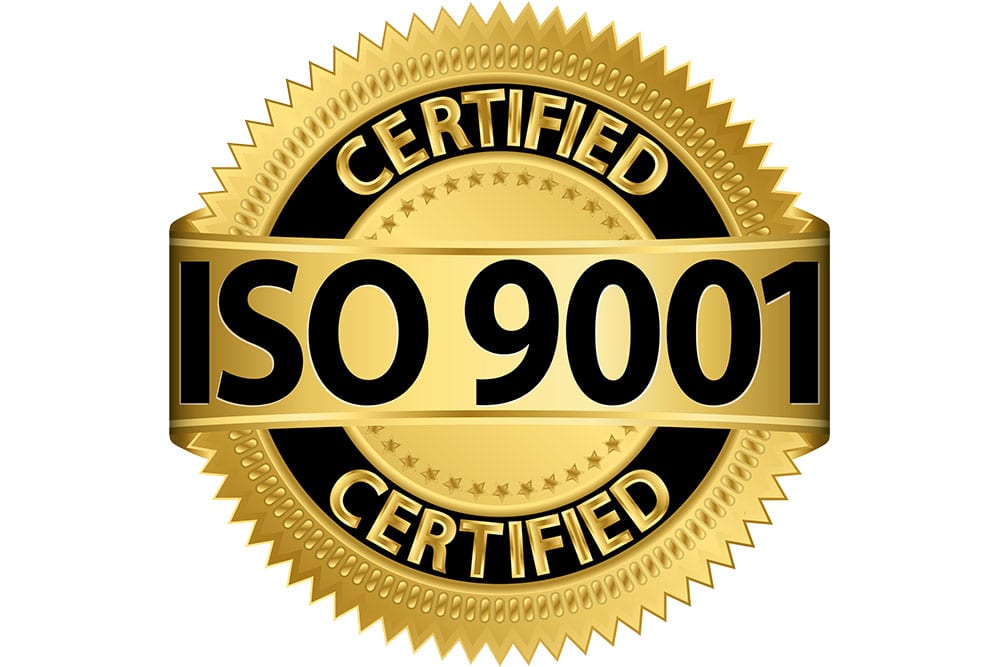
Gaining ISO 9001 certification can give manufacturers multiple benefits yet it can be an arduous process to get there. So, can using an enterprise resource planning (ERP) system help simplify the certification process?
What is ISO 9001?
Simply, it’s the world’s most recognised quality management system (QMS) and is generally regarded as the business excellence benchmark. Over 1 million companies internationally have achieved ISO 9001 in its current standard, ISO 9001:2015, or previous versions. Published by the International Organisation for Standardisation (ISO), it is a collection of policies, processes, documented procedures and records that are tailored by every individual company to define the way they create and deliver their product or service to their customer. ISO 9001 accreditation is often regarded as a guarantee that services and products are safe and reliable.
Companies that attain and adhere to ISO 9001 generally don’t need to be audited by their customers, making them a popular choice of supplier. Indeed, having a quality management system like ISO 9001 in place is often a pre-requisite to participation in the supply chain of major organisations.
Why else would we want ISO 9001 accreditation?
For so many reasons! A recent study showed that of companies who had gone through the ISO 9001 process:
- 57% felt it had attracted new customers
- 54% felt it increased their competitive edge &
- 65% felt it had inspired others to trust in their business
Top 10 reasons why manufacturers need a quality management system
Here’s why we believe all manufacturers need to implement and adhere to a quality management system like ISO 9001:
- Helps your company continually improve, streamline their operations and reduce costs
- Win more business and expand into different markets
- Improves your customer satisfaction with better quality products
- Reduces your business risk by helping you identify risks and minimise them
- Become more innovative
- Allows you to embed best practice into your company
- Better your company culture
- Increases leadership engagement
- Reduces product failures
- Enhances your credibility and customer confidence
Well worth the effort of gaining accreditation then!
What do we need to do?
A significant amount of the work around ISO 9001 is around defining your quality policy and objectives, before creating and documenting the mandatory and additional processes and procedures necessary for your company to create and deliver your product. This can be done internally although many companies bring in external help in the form of specialist QMS consultants.
Once policies, processes and procedures are defined and laid down, it is critical that these are adhered to. And that’s where using ERP for ISO 9001 can really help.
How can having an ERP system help a company achieve ISO 9001 accreditation?
An ERP system allows a manufacturer to develop a systematic approach to management, look to continually improve their processes and maintain a customer focus throughout – exactly how ISO 9001 companies should operate. In fact, in some industry specific standards, such as the automotive industry’s IATF 16949, having an ERP or MRP system in operation is now a mandatory requirement.
One of the greatest advantages an ERP system offers is the formalisation and standardisation of processes. With an ERP system, the same processes are carried out in the same way every time – exactly what needs to happen for ISO 9001.
An ERP system also supports continuous improvement as any non-conformances are quickly identified and steps taken and recorded to ensure the same issues don’t re-occur.
Another significant – perhaps the most important? – benefit an ERP system provides is that it brings all of your company’s data into one location. It is much easier to manage the processes below in one simple system than it is to cope with data being held on multiple spreadsheets or systems that can’t transfer data between them.
There are a number of key processes with a QMS that ERP systems like E-Max ERP effectively manage. These include (but are not limited to):
- Preventative Maintenance
- Document Management
- Traceability
- Non-Conformance Management
- Preventative and Corrective Action
- Calculating the Cost of Quality
- Process Control
Craig Metcalfe, Quality Consultant at Optimum Quality Management describes MRP and ERP systems as “the traceability glue that makes the implementation and management of ISO systems easy” and believes that companies who use ERP for ISO 9001 accreditation usually experience a more straightforward project as the key objectives of ERP and ISO 9001 are very similar. These goals of best practice standardised processes, strong customer focus and continuous improvement for top quality push organisations into becoming the very best version of themselves.
E-Max ERP is a flexible ERP system that has been designed to accommodate each individual company’s processes and can be used to help companies either attain ISO 9001 or to better manage their ISO requirements. For more information on this, visit our website, give us a call on 0141 644 4424 or drop us an email. If you’d like to see E-Max in action, schedule a free, no obligation demo of the system in action, you can book here.
If you’ve enjoyed this article, why not register to receive our monthly update on the latest industry and ERP trends?