Avoid costly mistakes with Bill of Materials software
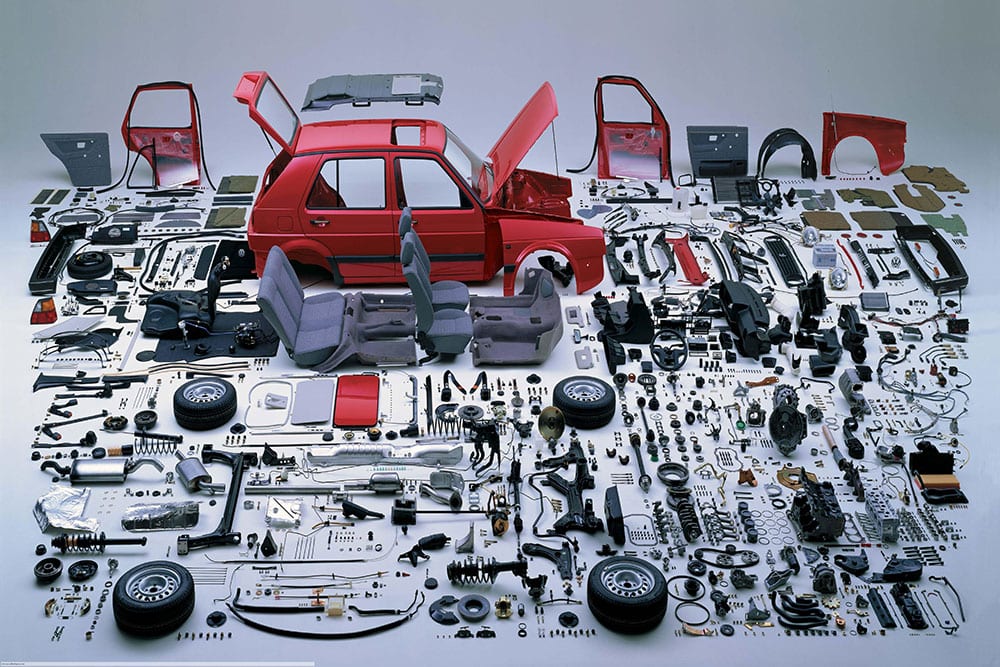
The Bill of Materials (BOM) sits at the very core of the manufacturing process. Getting it right is vital to avoid delays, costly mistakes and unhappy customers. With ever more complex products being manufactured, it’s no longer possible to rely on a paper-based process or spreadsheet to manage this critical element of manufacturing. More businesses than ever are seeking bill of materials software to manage their BOMs more effectively and reduce errors caused through manual input and duplication. So what should you consider when looking for bill of materials software options?
What is a BOM?
As most readers will be fully aware, a Bill of Materials (BOM) is a set of instructions that includes a list of all the raw materials, parts, items, assemblies and any sub assemblies (and the quantities of each) required to manufacture a complete product. It lays out all the information required to assemble or build a part. A good BOM will include what, how and where to buy the necessary materials, and will include instructions on how to assemble the product from the parts and materials ordered. It should also include any equipment and tools needed to build the parts.
If we’re getting granular, there are two main types of BOM – the engineering bill of materials (EBOM) and the manufacturing bill of materials (MBOM). The EBOM will include all the parts required in the original design, whereas the MBOM will include this information, as well as the additional parts, assemblies, tools and equipment required to build, assemble and package the finished product. Quality BOM software can import the engineer’s CAD design to build firstly the EBOM and then the MBOM, alleviating duplication and manual error.
- Building a bill of materials with E-Max ERP
Why is it so important to get it right?
Because a BOM sits at the very core of manufacturing operations and multiple departments will draw information from it – ie, purchasing, production, design, etc. – it is essential that the information in it is accurate and precise. The Bill of Materials impacts how much raw material you buy, your available inventory and the production process. If there are any errors or missed information, this could result in costly delays or even bring the manufacturing process to a complete halt. The last thing you want is for your production team to run out of the necessary inventory – a stationary shop floor is an expensive one!
But running out of inventory or materials is only one, albeit major, problem. Your production or assembly could also falter if the information in the BOM is not specific or clear. Poorly organised, out of date information or lack of detail within the BOM can create confusion and give rise to errors. A good quality BOM, on the other hand, will allow a manufacturer to produce their products efficiently and cost-effectively.
For companies that require traceability, a BOM system is a must-have as it tracks and keeps a record of every item used or manufactured.
What to look for in BOM software
There are some key pieces of information that should be included in your BOM at minimum. These include:
- Part number, name and description – to easily identify any part
- Quantity and Unit of Measure – to enable your purchasing team to calculate what’s needed
- Part type – is it purchased or manufactured
- BOM Level – for easy reading and interpretation of the BOM structure
- Notes – to provide relevant information for all involved
However, the more functionality and information you have in your BOM, the more efficient your manufacturing process will be. Look deeper into options such as:
- BOM copies – save time and effort by copying and amending existing BOMs.
- Costing – calculate the costs for each item in a BOM. Good BOM software will multiply the cost by quantities needed and factor in associated costs like tooling.
- Document management – the ability to attach documents, ie drawings, test certificates, etc to each part, item or material is a major benefit and allows all relevant personnel access to these when required.
- Engineering change control – track revisions and keep a trail of these for compliance purposes.
- Import functionality – pull in CAD designs to avoid manual input errors.
- Multi-level BOMs – combine items in your system to create a larger completed project. This is a necessity for those involved in complex manufacturing.
- Scrap management – calculate scrap quantities and allocate costs to this or flag non-scrapped material and return this to stock.
- Sundry items – add in any additional items required for manufacturing – this includes consumables such as moulds, glue, fasteners, etc.
- Supplier management – allocate a BOM supplier or preferred supplier for parts.
- E-Max ERP includes scrap management in the BOM
There’s no doubt that having good quality bill of material software helps a company manufacture their products more efficiently and cost-effectively. It also enables business growth. By focusing on accuracy and quality from the start of the process, manufacturers can increase production volume and scale their business. Plus, with a BOM system, you have all your production history to hand, with every change to parts or the production process itself recorded and saved. This information is very useful for audits and compliance reviews.
E-Max ERP’s Bill of Materials functionality includes all of the above features and more. To find out more about how E-Max ERP will make creating and managing your bill of materials a much faster and more efficient process, speak to our team directly on 0808 109 2035, message us today or take a look through our website. If you’d like to see how E-Max ERP calculates job costs, one of our specialists can take you through a no obligation demo.