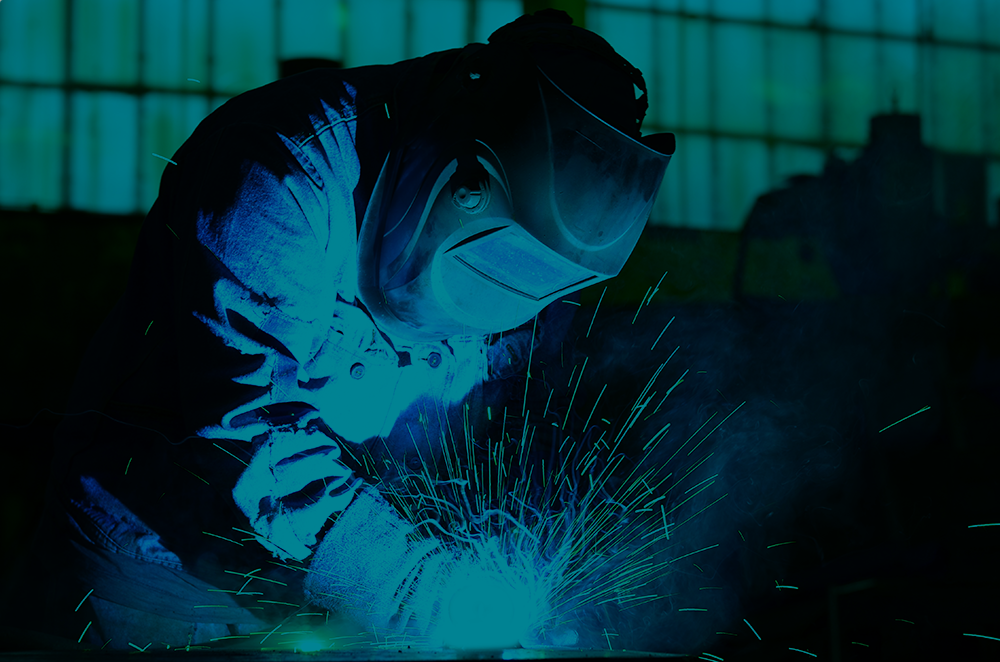
QA Weld Tech
<p class="fs-lg text-light opacity-70 mb-5">After a strategic business review, QA Weld Tech, a leading provider of integrated welding and engineering services to the oil and gas and petrochemical industries worldwide, were looking to improve their in-house information gathering and storage. Having identified that multiple Excel spreadsheets and Access databases across different departments were no longer sufficient to support the company’s growth, the management team sought a solution to enable them to bring all of QA Weld Tech’s data into one place. In an increasingly challenging economic environment, their objective was to use this information to make process improvements and create a more efficient company. <br><br>E-Max Systems were brought on board to provide a solution with their ERP software. Since implementing E-Max in 2012, QA Weld Tech have seen significant improvements in:</p> <ul class="fs-lg text-light opacity-70 mb-5"> <li>Decision making</li> <li>Provision of fast and meaningful data</li> <li>Time-savings all of which have led to numerous process improvements and improved production planning.</li> </ul>