Improve your Purchasing Power with ERP
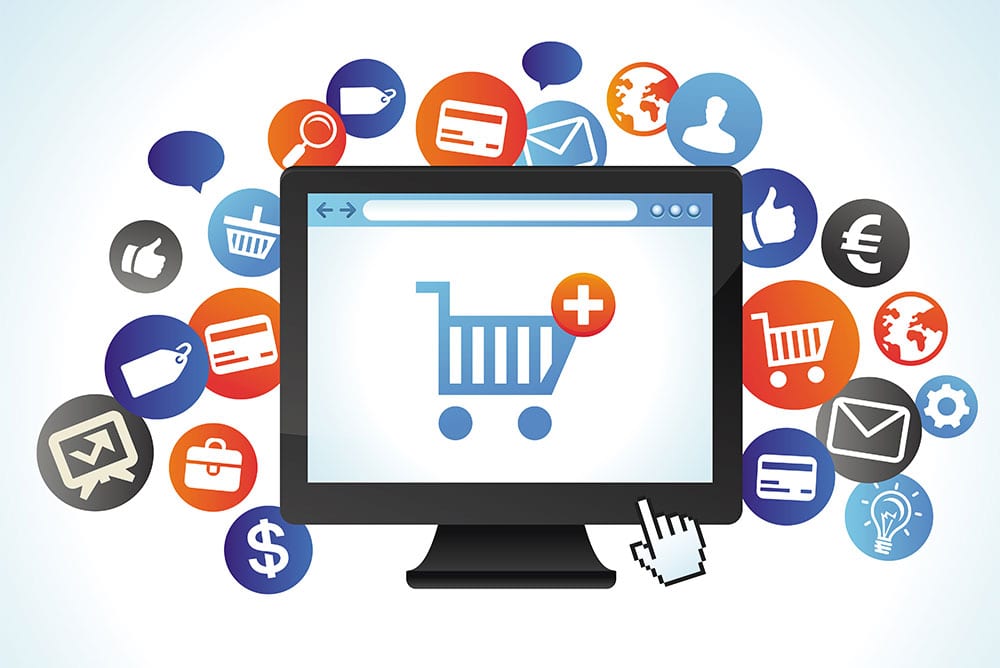
Most people know what an ERP system offers. In simple terms, an ERP will bring all your data together to enable better real-time decision making, streamline processes and allow your company to become more efficient. With these come the added benefits of facilitating company growth and improving your bottom line. It’s really a no-brainer as to why every manufacturer should have an ERP system in place.
So that’s the high level overview of what an ERP system can do for your company. But what separates out a great ERP system from a good one? We believe it’s all about the functionality, fit and ease of use. So it’s time to take a deep dive into various functions and features of E-Max ERP. In this blog (and future blogs throughout 2023), we’re going to get granular and look at key areas of our ERP system to highlight the functionality that’s available to our users. Register for our monthly updates to be sure you don’t miss out on these posts.
Why is Purchasing such an Important Function?
Purchasing or Procurement – call it what you will – is a vital function in manufacturing. Once upon a time, getting the lowest possible price was the main objective. With current supply chain issues and ever increasing fuel costs, purchasing managers must now also consider additional factors, such as quality, supplier reliability and delivery rates, when selecting where to place their orders. Purchasing materials is often the greatest single outgoing for manufacturers and getting your buying wrong can adversely effect your bottom line. Yet with the right tools in place, you can identify unreliable or expensive suppliers and minimise your risk.
A great ERP system collects and stores data on every aspect of the purchasing process and flows that information throughout your company. With this joined up approach it’s easy for purchasing personnel to identify and action any issues arising from purchased materials, whether it be quantities, quality or delivery timings.
7 Clear benefits E-Max’s ERP Purchasing Module offers manufacturers
• Clear visibility of ALL requirements across your business
• Ability to manage your supply chain effectively
• Easily identify late items and manage production accordingly
• Clear reporting on supplier performance
• Clarify job costing as you buy and allocate costs to specific jobs
• Reduce duplication by easily requesting quotes from multiple suppliers
• Stay focused on what’s important with our intuitive Purchasing Dashboard
How does the E-Max ERP Purchasing Module work?
Once an order is received and the necessary works orders raised, it’s time for your purchasing team to leap into action. E-Max ERP makes it easy for purchasing staff to identify what is required and when it is required for.
Using the pre-set filter, PO Required by Delivery, users can view details like Item Code, Date Required, Quantity Required, Preferred Supplier, Lead Times, Stock Status, Last Purchase Price, Last Purchase Date, etc, for each item required . Our Create Order function allows you to raise and send a purchase order in just a couple of clicks. Alternatively, should you decide to manufacture it in-house, a works order can be raised from the same menu instead and will then feed the required materials back onto the PO Required by Delivery list (see below) for order.
E-Max provides various supplier options when raising your PO. The pre-populated Preferred Supplier field is understandably the most frequently used choice. A BOM Supplier is available when our customers have linked a supplier to a Bill of Materials or users can choose another new or existing supplier. It’s also simple to raise multiple Requests for Quote from suppliers – simply create a Request for Quote, add the items you wish to be quoted for and then multi-add the suppliers you want to send the quote to. The system automatically creates a number of individual purchasing quotes so you can record the prices for easy comparison when you receive the quotes.
Supplier history is displayed, showing all previous orders, when they were placed and pricing for each. Any previous special offers are also shown – allowing you to request repeat special rates! Price break quantity information is also stored.
Once the PO is raised, E-Max ERP creates a Purchase Receipt to be used for the corresponding incoming deliveries. This allows Purchasing and Warehouse Management to plan and prepare for the items coming into stock and follow up on the delivery progress of these to ensure they are on track for on time delivery.
There is full visibility of all open Purchase Orders (PO). If another item needs to be ordered from the same supplier, a new line can be added to the existing POs to reduce delivery charges. Late POs can also be easily identified.
Purchasing approvals can also be set and security roles applied to control purchase levels. Purchase orders can be raised in the usual way but cannot be released until authorised by a nominated Approver. Any POs requiring approval automatically appear on an Approvals Required list and can be easily identified and actioned.
All of the above information can be viewed from each user’s dashboard, allowing your Purchasing team to focus on their KPIs.
E-Max ERP contains more intelligent purchasing functionality so if you’d like more information on this or anything else relating to E-Max ERP’s functionality, please visit our website, give us a call on 0808 109 2035 or drop us an email. If you’d like to see E-Max in action, schedule a free, no obligation demo with us and see how our wide range of features really can make a difference to your business.