Scheduled Maintenance with ERP Reducing unplanned downtime
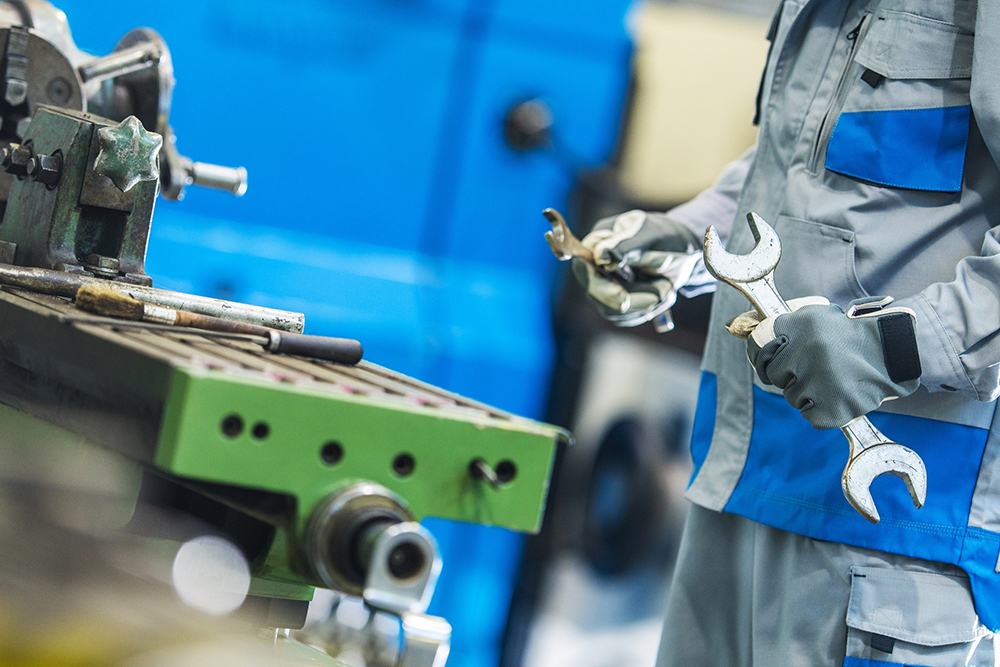
Maintenance can be a tricky process in manufacturing. Unexpected downtime causes delays in production and increased costs, as well as raising the stress levels of everyone involved! Whilst it’s virtually impossible to avoid any unscheduled maintenance, manufacturers who develop and stick to a robust maintenance plan can reduce unplanned outages and save themselves a great deal of trouble.
Why is Maintenance so important?
In this competitive age, it’s vital to keep your machines operating at the highest level of efficiency at all times. And whilst increased costs and disruption are big issues that you most definitely want to avoid, there are plenty of other long term benefits to be gained from preventative maintenance, including:
- Improve safety around the workplace and minimise the risk of incidents
- Avoid expensive emergency repairs that arise from negligence
- Reduce your energy and operating costs with equipment that runs efficiently
- Prevent small issues growing into big issues with regular checks
- Extend the lifespan of equipment (reduce the need to purchase new equipment)
- Increase resale value of equipment with full service history
- Keep your warranty cover with detailed service history showing you are up to date with maintenance
Following a planned preventative maintenance approach is an effective form of facility management and enables you to avoid delays and interruption of regular work orders, as well as better managing your tools. Pre-planning your maintenance makes it easier to budget and plan around.
Using ERP for Scheduled Maintenance
Short daily inspections, minor tasks like cleaning, lubricating or making small adjustments, and full-scale servicing all need to be undertaken at certain times to ensure your equipment operates effectively. However, the timing of each of these is critical. Finding the optimum time for these activities is important to minimise disruption and have the least impact on the manufacturing process.
Using an ERP for scheduled maintenance gives you the opportunity to identify these optimum times. An ERP system gives you a 360° view of what is happening in your company. This enables you to plan your maintenance activities to avoid any clashes with scheduled work.
ERP also makes scheduled maintenance a quicker and easier process to manage because information on your machines, tools and other equipment is already in the system. It is a simple matter to raise works orders for any tasks associated with tool or machine maintenance and schedule them in line with all other operations/tasks to be carried out. These tasks can be automated to ensure they take place on a regular basis, whether that’s daily, weekly, quarterly or annually, making it easy to meet any warranty requirements.
Managing your maintenance programme in your ERP system also allows you to keep track of all maintenance activities. A full history of all associated tasks, dates and resources, including personnel, is securely stored and easily accessible to review. This information can be used to identify trends, spot problem areas and work on solutions for these.
E-Max ERP supports Scheduled Maintenance programmes
You can create and manage regular and on-going maintenance schedules in E-Max ERP. These schedules can be applied to all assets, work centres, tools and even facilities, like kitchens, communal zones and storage areas – in fact, any area that requires maintenance can be tagged on E-Max ERP. Once an item is identified as needing maintenance, E-Max ERP opens up multiple options for activities that need to be completed as part of a maintenance programme, such as visual inspections, oil and fluid checks or parts replacement.
E-Max ERP records and manages:
- Full service history
- Service periods
- Next service dates
- Last service dates
- Service items
- Instructions
- Stock issues to maintenance orders
- Incident logs
The functionality behind the above features means that any maintenance requirements will be linked directly to other areas of E-Max, and in particular to purchasing and stock. This allows you to manually or automatically raise internal works orders and/or external POs for contractors to undertake these maintenance tasks. These tasks can also be linked to our shop floor data collection (SFDC) so that time spent is recorded and the total cost of maintenance can be calculated.
E-Max ERP also has a dedicated maintenance dashboard which can be tailored to your requirements and enables actions, tasks, cost of maintenance and safety KPIs to be easily monitored.
To find out more about how else E-Max ERP can help you manage your scheduled maintenance programs more effectively, chat to our team on 0808 109 2035, drop us a message or visit some of the other areas of our website. Of course, if you’d like to see for yourself what else E-Max ERP can offer your business, then our team would be happy to arrange a no obligation customised demo at a time convenient to you.