Is ERP Worth It?
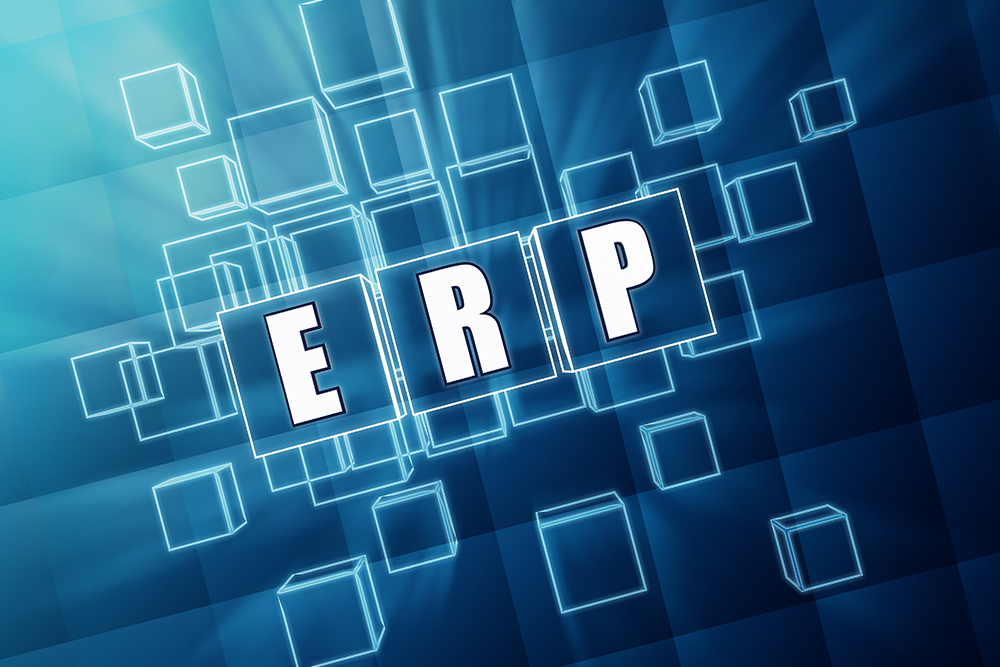
Deciding whether or not to implement an ERP system can be a tough decision for SMEs. You’re managing with your existing systems and processes but let’s face it, there is probably room for improvement. Silly manual errors happen, trying to pull out useable information from multiple spreadsheets or legacy systems proves time-consuming and demanding, and, whilst you have a reasonable idea of your inventory, things occasionally grind to a halt as someone frantically tries to locate the elusive item or material that you think you have but need NOW!
You know ERP makes sense with all the benefits it offers but, on the flip side, you need to consider the costs, resource implications and potential disruptions that will come with the new system. So is an ERP system worth investing in?
Here’s why ERP really is worth the effort
1. Become more competitive
If you’ve read any of our other blogs, you’ll know we firmly believe that an ERP system gives businesses a competitive edge. At least, it allows you to keep up with your competitors and at best, it puts you far ahead of them. Maintaining that competitiveness is a critical success factor for manufacturers.
Whatever your USP is, whether you are competitive on price, quality or delivery, an ERP system will provide you with valuable insights to help you excel in each of these areas, whilst the functionality embedded within an ERP will enable you to make the most of your resources and cut down on waste and costs.
2. Increase your operational efficiency
Unfortunately, in manufacturing or engineering, there are plenty of opportunities for waste. Having an ERP system to streamline and automate processes leads to a significant reduction in waste, including duplication of effort, manual errors and paperwork overload. Personnel are freed up from time-consuming, routine manual tasks, and can concentrate their efforts on activities that bring more value into your business.
An ERP system is also an excellent tool for identifying other areas where business process improvements can be made. This could be as straightforward as moving the location of a frequently used tool or a more complex process change involving a new sequence of tasks but, either way, will enable your business to reap the rewards of increased production efficiency.
3. Better reporting and decision making
Moving all your data from multiple (and often inaccessible and non-compatible) systems or spreadsheets into one ERP system gives you a true picture of what is happening within your organisation. Not only is this information accurate, it is also available in real time. This gives you the opportunity to respond promptly to issues and capitalise on opportunities as they arise, making your business more agile.
Many ERP systems offer users the option of creating a dashboard of key performance indicators (KPIs) and analytics, for greater focus on what matters most to them. A single screen with live ‘at a glance’ data is invaluable in for smooth day- to-day operations. Even more value can be obtained from the reports an ERP provides, containing details of current and future trends, demand forecasts and financials. It is this information that allows management to make critical decisions and advance your business and for this reason alone makes implementing an ERP system truly worth doing.
4. Improve supply chain management
The Covid years highlighted how crucial robust supply chain management is. An ERP system manages the manufacturing process from end to end, starting with the sourcing of raw materials all the way through to final delivery. Managing all the complexities of this process in one system means greater efficiencies can be realised, and provides clear visibility throughout the supply chain.
Once a job is scheduled in line with delivery requirements, an ERP system will check the materials for the job are available, creating alerts or POs if not. Manual tasks, such as communication with suppliers, tracking of material delivery, and more, can be automated. Delivery notes are also automated and stored in the system. As soon as the goods are despatched, the invoice is automatically created and sent. Traceability details are recorded within the system.
Inventory is also managed more efficiently with an ERP system. Stock levels can be kept lean and inventory is moved effectively, using methodologies like FIFO and LIFO where applicable.
5. Benefit from company-wide collaboration
When an ERP system is implemented, silos are broken down and there is an increase in collaboration across departments and the company as a whole. Taking a new order as an example, it’s easy to see how ERP makes this collaboration simple. From your Sales team taking an order and updating your ERP system, all relevant departments (or individuals) are notified about the tasks they need to perform. Your Purchasing team will know what materials you have in stock and what need sourced and bought in; Production will see that the job is confirmed, schedule it in and confirm they have the resources available for the job; the Warehouse team knows when to expect goods in and when the finished product needs to be shipped; and finally the Accounts department knows when to raise the invoice.
An ERP improves communication company wide and ensures everyone is pulling in the same direction. All departments can see the whole process and can understand where they fit into it, fostering a feeling of being part of a unified team. Delays between stages in the process are removed as each individual or department knows what to do and for when.
The standardisation of data across the system is also a huge benefit. No more trying to transfer raw data from one department to another in different formats, making analysis difficult. Everyone is using the same data – effectively speaking the same ‘language’, allowing for much more effective communication.
Why an ERP system might not be worth it
1. It’s expensive
It’s true – a high-quality ERP system doesn’t come cheap. But the cost savings one provides mean that with the right solution, your ROI could be achieved in as short a timescale as 6 months post implementation. The most significant savings are generally seen through significantly improved inventory management and resource savings through streamlined processes and removal of duplicated effort.
2. There are resource implications
Identifying and selecting the right ERP system for your company takes time and effort. Most companies involve several employees from different areas such as finance, production, purchasing and sales in the decision-making process. Once a decision has been made, it’s strongly recommended that companies appoint a champion to drive the project (otherwise it’s never anyone’s top priority!) This resource does add up and means people are diverted from their primary role, potentially leaving gaps within your company.
The plus side of this however is that if you have someone effectively driving your project forward and working with the ERP provider on a regular basis, implementation times are greatly reduced and you can start to see the ROI on your new ERP system much earlier.
3. You will experience some disruption to business
The ERP implementation process is generally time consuming. Process analysis, scoping and data imports will all require involvement from multiple employees across your company. Streamlining processes and making changes is often met with resistance from other employees as the natural fear of change kicks in. In addition, time needs to be allocated to training your workforce on how to use the new ERP system. There is a learning curve but with strong management, good planning and effective communication, these issues can be resolved. The resulting gains – for both the company and each individual – will outweigh these challenges.
Conclusion
So, is ERP worth it – and by ‘it’, we mean the challenges and effort required to successfully implement and use? We certainly think so and have seen hundreds of companies transform themselves and grow with ERP. If you’d like to find out more on how E-Max’s software has helped other manufacturers or engineers, take a look at some of our case studies on our website, or speak to one of our ERP consultants on 0808 108 2035. To see E-Max ERP in practice, simply click here and one of our consultants can provide a short run through of how E-Max works.