Simplify stock control in manufacturing
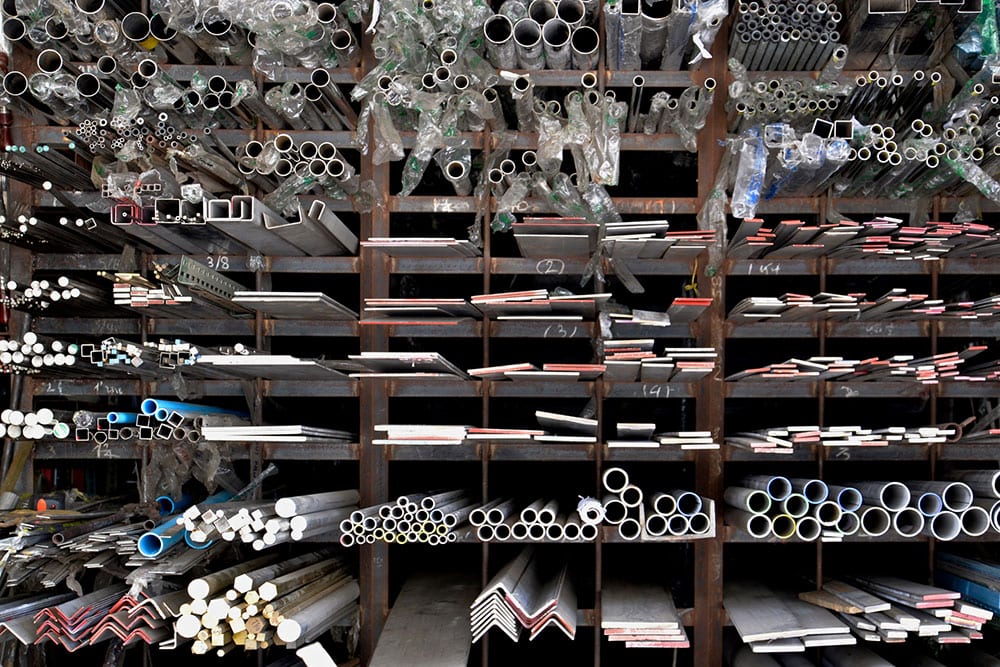
Stock control in manufacturing shouldn’t be difficult. All you want to know is what’s in stock and where it is. Any simple stock control system should tell you that, right? But unfortunately, it’s not always as easy as that. Not all stock control or warehousing systems are created equally, so finding one that handles all aspects of your manufacturing requirements can be a challenge. In this blog, the next in our series of exploring E-Max’s features, we look at how effective stock control (or warehouse management) is fundamental to the success of manufacturers and how the design and capability of our stock control functionality is making life a whole lot simpler for our manufacturing clients.
Stock control in manufacturing
Bringing the concept back to its most basic level, stock control is a matter of taking delivery of goods from a supplier and then getting these goods out to your customer as per diagram 1.
Manufacturers add an extra level of complexity to this process (diagram 2) in that they usually need to manufacture the end item. It is because of this extra layer that many non-specific stock control systems fall short of providing the information that manufacturers need to keep their orders running through their business smoothly.
6 common stock control problems faced by manufacturers
Because of this extra complexity in the stock control process, manufacturers experience some unique issues. These are the most frequently expressed complaints we hear from manufacturers – do you suffer some or all of these pain points?
- No visibility of stock – knowing what you have, how much of it and where it is
- Managing offcuts – how to get them back into stock
- Unnecessary wastage costing money, ie consumables
- Traceability – knowing what materials or parts are used in what finished items
- Cash flow implications – cash tied up holding excessive stock
- Incoming material deliveries – making sure that purchased material for a job still arrives on time if the delivery date of the job were to change
The good news is that E-Max’s stock control module is designed to handle and resolve all of these problems!
What information can I get from E-Max’s warehouse management system?
A simple stock control system should tell you what you have in stock and where it is. E-Max’s stock control goes much further. We’ve taken into account the need of manufacturers so not only does E-Max clearly shows what’s in stock and where it is but also shows you what you need to buy, when you need to buy it for, as well as what you need to make, and for when.
With multiple screens and drill down ability in every field, you can easily see specific parts or materials. Two of the main screens at the heart of our stock control module are Purchase Orders Required and Work Orders Required. From these, you can drill down to see the orders that are creating the requirements. This makes it easier to plan and prioritise purchasing and manufacturing.
- Purchase Orders Required allows you to see everything you need to purchase on a single screen
- Work Orders Required allows you to see what needs to be manufactured
You can also access current orders and track the dates stock is due to arrive and even its current location – ie is it still on the water, at customs, etc. E-Max recognises supplier shortages and back orders and automatically creates additional deliveries to allow you to manage these.
Another significant screen is your Current Stock List. This can be searched in multiple ways to find stock you already have to fulfil both manufacturing and sales requirements. This list can be set up to show whatever information is most relevant to your business, be it serial numbers, quantities, material specification or original supplier.
- The Current Stock List can be customised to show the fields most important to your business
In short, E-Max provides complete visibility of all your stock and requirements.
What other features does E-Max’s stock control offer?
Our stock control module includes all the functionality required to manage your stock and more. As well as the standard features you’d expect to find in a stock control system, E-Max offers additional capabilities. We’re highlighting our customers’ most popular features here but if there’s any other functionality around stock control in manufacturing that you want to know about, just ask.
Stock records created in advance of deliveries
When stock shortages are identified and a PO raised, E-Max creates a stock record. The stock won’t show in the system until the delivery is received but the stock record will. This allows you to record against delivery batches any test certificates, serial numbers, drawings or revisions, etc, that you receive in advance of the actual goods being delivered. Planning and quality departments can store and check relevant documentation prior to delivery, thus simplifying and speeding up goods-in procedures.
- Stock records are created even before stock arrives so data can be stored against them
Complete traceability from delivery in to delivery out
As you would expect, E-Max offers full traceability throughout, from as early as raising the original PO. For companies that work with consumables, FIFO, LIFO and Use by Date options ensure that materials are used in the optimal manner. Manufacturers who operate in regulated industries and/or are contractually obliged can also utilise the Serial and Batch traceability options within E-Max. E-Max also includes a full stock posting history so it is easy to see where stock has been and what happened to it.
Multiple warehouse functionality
Ideal for companies that have more than one site and stock moving between them. Stock can be viewed across different warehouses and locations, different bays, racks and zones, allowing companies to see what they have in stock and where exactly it is.
- Knowing exactly where your stock is allows you to plan to get it to where it needs to be on time
Automatic allocation of stock dependent on size
Rather than piling offcuts in an area of the warehouse where they are never used due to lack of visibility as to what’s there, E-Max offers an easy way to store and track excess materials and reduce wastage.
This feature allows offcuts of any size to be returned to stock. Length, width and height dimensions of shelves, bays or bins can all be set on E-Max and items within these parameters will be stored in specific locations. Offcuts are then stored in E-Max as usable and available materials, with any serial numbers or certificates linked to them.
Full visibility of all categories of stock, including virtual stock
Ideal for companies that work with blanket orders or call-off orders, this feature allows you to see the quantities of ALL stock, regardless of status. This means that you can view on a single screen what is
– currently on order
– in production
– in stock in the warehouse
– in demand (orders)
– the resulting level of stock, ie what you will be left with
- View quantities of each item of stock, even allocated or on order stock
This visibility enables you to identify any shortfalls against blanket orders and is also a useful tool to prevent cash flow being tied up through excessive levels of stock.
Stock ownership
Not all stock that moves through your warehouse may belong to your company. Customer or supplier owned stock can be delivered and tracked, using the same functionality as purchased stock. This is particularly useful for repair items or consignment stock and enables better planning for these situations.
- Our stock screens can include stock owner, batch and serial numbers
Delivery and Returns management
It’s simple to plan for every delivery with a dedicated screen that provides you with information on every scheduled delivery. This means you can manage and plan your deliveries effectively, ensuring that you have the necessary resource and personnel on site as required. Returns are also visible on E-Max and can be scheduled as an incoming delivery, then their progress tracked.
- See information on every scheduled delivery
E-Max’s stock control software has been developed specifically to help manufacturers and engineers get full visibility of their stock and manage it efficiently. If you’d like to find out more about E-Max’s stock control functionality, visit our Warehouse Management page, call us on call us on 0808 109 2035, or email us. You can also see E-Max in action by arranging a free, no obligation demo with us and see how our wide range of features really can help streamline your business.