Manufacturing for Oil & Gas – 6 must have features for your ERP
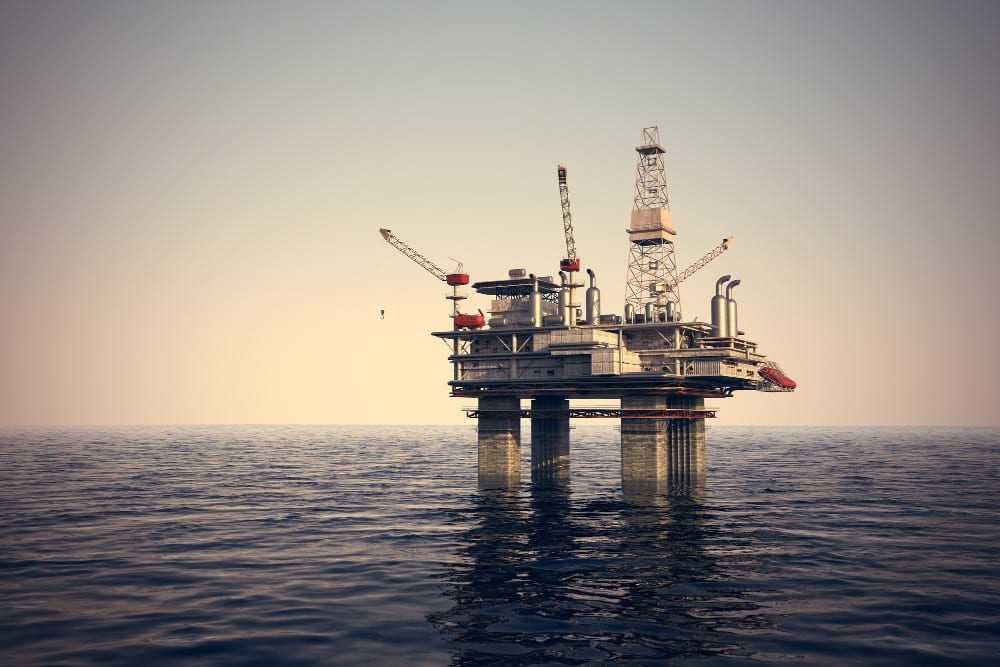
The oil and gas market has encountered challenging times recently, facing an unprecedented drop in demand and the global pandemic crisis. Excess supply and rock bottom prices have shaken the oil and gas industry to the core. But it’s not all doom and gloom. The industry is showing signs of recovery, with an upsurge in demand and oil prices on the rise again. Despite advances in alternative fuels, it’s safe to say that the oil and gas industry is likely to be around for the long term and it’s no surprise that many manufacturers are keen to get involved in the supply chain for this profitable industry.
If your business is in – or wants to be in – the oil and gas supply chain, you’ll need an ERP system. Most oil and gas companies will have standards that need to be complied with and any new supplier will need to convince a potential customer that they have effective systems and processes in place before winning a contract. An ERP system is a key indicator that a company already has the mapped out, efficient and streamlined processes demanded by oil and gas companies, and may even be a requirement in a tender document. Without an ERP system, you may not be qualified to bid on contracts. But what features of an ERP system are a necessity for success in the oil and gas supply chain?
#1 Support for quality and safety accreditations
In this sector, there’s generally a requirement for suppliers to have certain accreditations. With an ERP system, your processes are standardised and documented, making it simpler to attain and maintain Q & S accreditations such as ISO 9001.
#2 Traceability of parts and materials
Although not as regulated as some industries, such as aerospace, having traceability on all parts and materials is a necessity. Having multiple traceability options in an ERP system is an advantage. Batch, serial, cast number and heat number are all valid and useful to have. In systems like E-Max ERP, these details can be recorded prior to the raw materials reaching the warehouse and tracked throughout the entire manufacturing process through to shipping and delivery at the customer. This history can be accessed at any time.
#3 Recording and generating Certificate of Conformity and test certificates
Items that you produce for your customer may require a CoC to state that the product meets the required standards or specification. An ERP system should be able to generate a CoC and test certificates as needed. If tests have to be conducted externally, these test certificates should be able to be linked to the part and stored within the ERP system for any future reference.
#4 Part and drawing revisions
It’s not uncommon for there to be several changes made to plans and specifications for bespoke parts. An ERP system needs to record when a part has changed, when it was amended, by whom and why. It should also clearly highlight the current revision so that mistakes are avoided.
#5 Project management
Oil and gas projects are often complex and multi-layered. Key parts may need to be manufactured in stages before a job can be assembled in full. It’s therefore vital that your ERP system can calculate when parts are needed and ensure that each element of the project is tracking on time to meet the customer deadline.
#6 Record keeping
An ERP system should hold all records of each job securely and in one place. There may be a requirement from a customer that records are kept for upwards of 7 years. These can be backed up and kept safely for as many years as required with little to no risk of loss or accessibility.
Of course, an ERP system should offer much more functionality than these 6 features! Find out more about the other benefits you can expect when using E-Max ERP for oil and gas supply chain manufacturing by speaking to our team on 0808 109 2035, messaging us or visiting our website. If you’d like to see E-Max ERP in action, one of our specialists can also take you through a no obligation demo.