Using ERP to Continuously Improve Efficiency
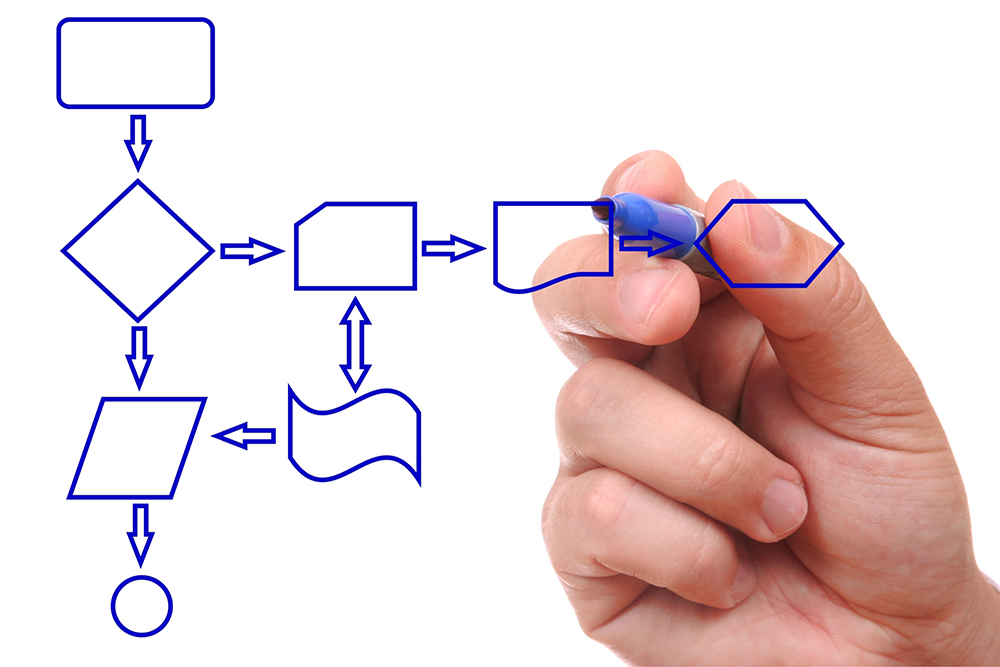
Implementing an ERP system will allow your business to streamline processes and achieve greater efficiency immediately. But there’s always room for improvement. In fact, Lean methodology recognises the quest for perfection to be never-ending. Fortunately, with an ERP system in place to support Kaizen (or continuous improvement), it’s a lot easier to keep increasing the efficiency of your processes. Let’s take a look at some recent examples we’ve come across and see how using your ERP system effectively supports continuous improvement and efficiency gains.
Use Stock Control to Manage Offcuts Properly
Offcuts are often a big issue. Some raw materials can be costly and waste is never good so getting offcuts back into stock should be your standard operating procedure. But offcuts can be tricky to manage as they don’t conform to a specific size. We find that many manufacturers do try to save their offcuts for later use but when the moment arises that they need them, specific pieces are impossible to locate. Time is spent trying to track them down and often the easiest and most efficient way of progressing the job is just to use a standard piece of material, ie a new sheet or bar. So how can this process be improved?
Using an ERP system to identify a location for offcuts in your warehouse or stores is an easy option. When the spare material or offcut is collected, it’s a simple matter of logging it back into stock on your system and noting which bin or area it is to be stored in. E-Max ERP allows offcuts to be included in stock and records the measurements in terms of breadth, length and height. The location is also recorded so next time you need that extra piece of material, it can be identified and located in no time at all. If you don’t want this included in active stock, a quarantine location can also be added so that it’s still on the system but not impacting your stock levels. Items or materials stored this way can also be added back into stock (with full traceability) and allocated to a job via the route card. Improvement #1!
Set up a Relevant Focused Dashboard
Effectively using a dashboard to review information will make users better at their job and more efficient. To do this, dashboards need to be focused on the KPIs that matter. Let’s use the example of the warehouse or stores’ manager again. His or her daily responsibilities include booking stock in, ensuring stock goes to the correct location in the warehouse and getting materials/or tools to the right work centre or machine in time for the job to be started. There’s a lot to manage and often a significant amount of stress associated around these activities – we all know living in a state of constant stress is not an efficient way to work.
Creating a personalised dashboard in an ERP system that drills down to the specific activities that need to be carried out that week, day or even hour, enables focus and better use of time and resource. Your stores manager knows exactly what needs done and when and it’s not until that dashboard is at zero that everything is completed. But once the magic zero is achieved, the stores manager becomes a resource with time at their disposal. An extra pair of hands never goes amiss, whether it is for the small jobs, like directing a forklift, or the more significant activities that do result in efficiency gains, like working on 5S or performing a stocktake.
The dashboard can be used by most workers in the business to ensure they are carrying out the tasks that need to be done to keep the workflow progressing smoothly. Improvement #2.
Identify Areas of a Process That Aren’t Effective
Our final example of using ERP to continuously improve efficiency in the workplace comes from one of our manufacturing customers. Their stores manager had developed a process whereby all stock was booked out in the last 15 minutes of the working day. This suited him perfectly as he was able to use the spare time to change out of his work boots and be prepared to head home the moment the clock hit finishing time. However, did it benefit the company in the same way? Most certainly not. By making adjustments to stock at the end of the day, any issues, such as low or no stock, couldn’t be actioned until the next business day. Instead, booking the stock out throughout the day means that stock issues would be flagged in business hours, and appropriate action taken, such as a PO being raised and sent to suppliers.
Once this issue was identified, the process was amended so that stock was booked out at the time of allocation. Instead of changing his boots, the stores manager was able to use the time more effectively by preparing items for the following day’s jobs. Improvement #3.
We’ve just picked a few areas where our customers have been able to improve efficiency with an ERP system but there are countless other examples. An ERP system gives you the visibility to identify areas where you can make efficiency gains and continuously improve your processes – both significantly and marginally. If you’d like to find out more about using ERP to continuously improve efficiency, why not have a chat to our team on 0808 109 2035, drop us a message or visit some of the other areas of our website. We can also show you E-Max ERP in action at a time convenient to you.