Using ERP to understand job costing
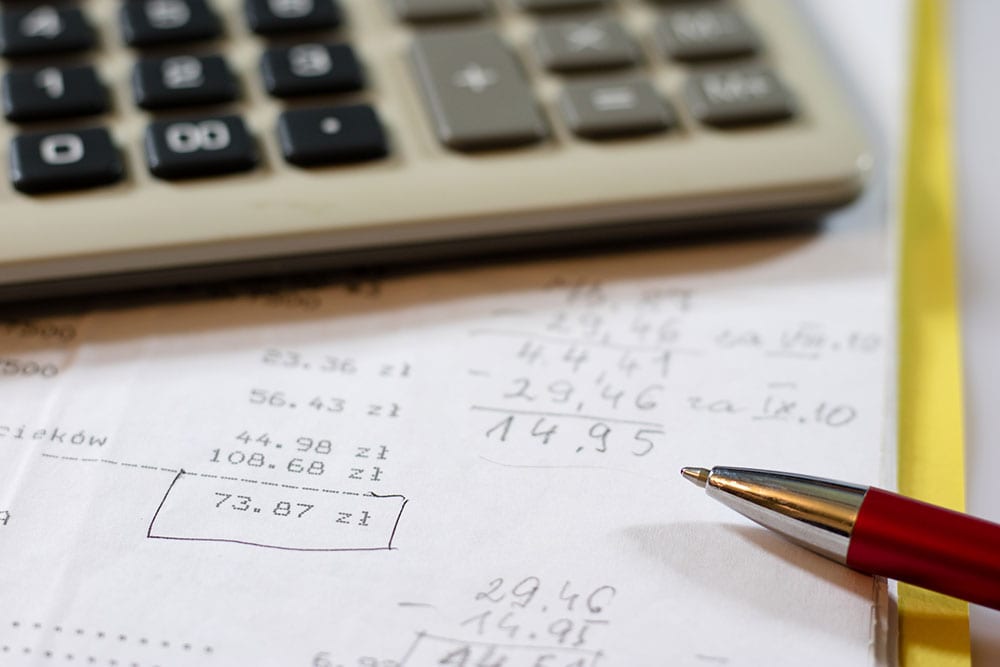
Most engineering or manufacturing companies we speak to want to get a true picture of which of their jobs are making money, and, of course, those that aren’t. Often, as it stands, their current ‘calculations’ are based on gut reaction, past experience and the fact they are still in business. It’s less likely to be based on detailed understanding of job costing, pricing and margins unfortunately. Imagine if you could:
- Track your costs in real time for every job on the shop floor?
- Use real-time costing to spot areas where you can cut production costs and increase your margins?
- Know your costs per quantity (single part, 100, 500, etc) so you can calculate what quantities are the most efficient to make?
- Use your cost and margin knowledge to undercut competitors yet still make money on the job?
The good news is that with an ERP system you can.
How does E-Max ERP help with job costing?
E-Max ERP is designed to collect your costs accurately
- It records the actual cost of material and any subcontract items against each job
- Purchase Variances and Landed Costs are automatically allocated to jobs
- Records labour and machine usage costs on shop floor data capture against each job without the trouble of entering timesheets
- The cost of rework and Non-Conformances will also be allocated to the relevant job
- Capture design, programming and prototyping costs before a job goes live and link these to the original enquiry and opportunity. Sample costs can also be added to a job.
- Every single cost going through your company such as tooling, expenses and consumables can easily be allocated to the correct jobs
Cost reporting and analysis
Return per Machine Shop Hour
E-Max ERP offers a report to calculate revenue generated per hour worked. This report makes it incredibly simple to compare jobs, even if one job uses a lot of expensive material and another uses no material at all. This report enables you to identify whether you are charging enough to break even on a job.

E-Max offers multiple reports to track and analyse your job costing
Profit by Contract
This is a very popular report. Many of our make-to-order manufacturing customers swear by this one! It allows you to flag variances between planned vs actual costs and get easy drill-down on any of these variance. Review factors like: did you save on hours worked but have higher than anticipated material costs? Were these costs higher due to exchange rate fluctuations or was more material needed? Perhaps the quantity break pricing from a supplier wasn’t considered – did the customer originally ask for a quote for 2000 but eventually only ordered 500?
(NB To avoid this last scenario reoccurring, a contract review can be set up in E-Max which creates alerts to flag variances on an order from an original quote. This is particularly useful in the event of price increases and can be set to require manual approval so the materials cannot automatically be ordered until the new pricing is reviewed and approved.)
Additional benefits of using ERP for Job Costing
In open book relationships with customers the visibility ERP provides enables companies to share their cost information with the client so they are more accepting of increases.
Whilst job costing is a vital element in the armoury of any manufacturing or engineering company, it is also important to ensure that your company gets enough of the right kind of work to cover your overheads and make good profits. E-Max’s job costing software provides that essential visibility.
Using an ERP for job costing allows you to identify variances and take appropriate action. Find an alternative supplier, don’t be surprised by higher prices, understand why more resource was used than expected so you can factor that into your pricing in future. With this information you can set margins and pricing to enjoy profitable work, yet still remain competitive when you need to. E-Max ERP helps you make the right financial decisions for your business.
Find out more about how E-Max ERP will help you track and analyse your job costing by speaking to our team on 0808 109 2035, messaging us today or visiting our website. If you’d like to see how E-Max ERP calculates job costs, one of our specialists can take you through a no obligation demo.
If you enjoyed this blog, why not check out other E-Max blogs that may be of interest:
Case study: Tarvin Precision: Getting transparency of costs
The importance of Material Requirements Planning in manufacturing