Improve supply chain management with an ERP system
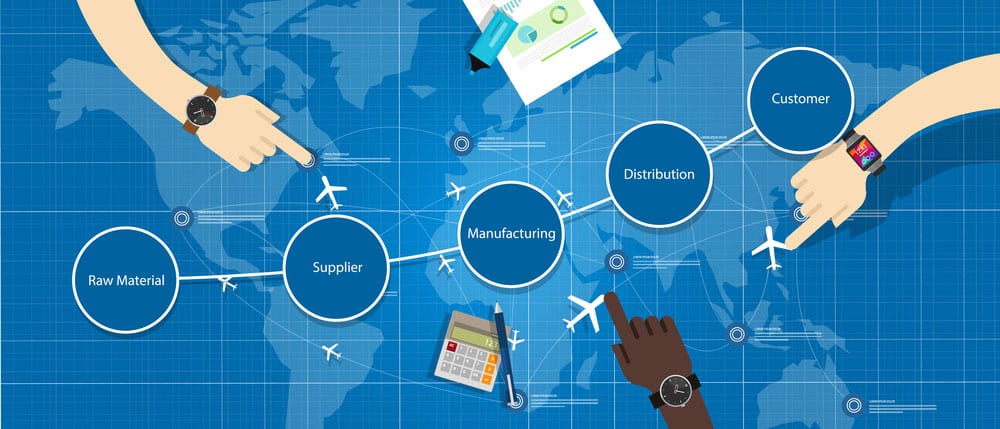
Every manufacturing company that we work with operates in a supply chain of manufactured goods/products and support services with an aim to develop business relationships that mutually benefit their customers and suppliers. Information is a key factor in the success of supply chain management, necessitating a quick and constant flow of information between all parties.
Effective management of this supply chain is crucial as an optimised supply chain leads to lower costs and a faster production cycle and provides companies with a competitive advantage. A well-managed supply chain can be the key to improve margins, drive positive customer experiences and support company expansion. A poorly managed or inefficient supply chain will result in duplication of effort, unnecessary paperwork, and slow response times. Consequently, improving supply chain performance is a common business objective. So how can integrating ERP and supply chain management make a difference?
What is the supply chain?
Defined by Wikipedia as “a system of organisations, people, activities, information, and resources involved in moving a product or service from supplier to customer”, the supply chain includes all activities from the delivery of source materials from suppliers to the manufacturer through to the eventual delivery to the end user.
For a manufacturing company, this supply chain structure includes all functions and processes from enquiry to invoice e.g. enquiry, quotation, product development, marketing, production, purchasing, distribution, finance, customer service, etc.
The supply chain also includes all the activities linked to customers and suppliers that are required to fulfil a customer request, i.e. incoming or outgoing deliveries, purchase orders, stock levels, subcontractors, etc. It’s a fair amount of activity to organise!
Fortunately, the rise of integrated business software, automated systems and high-speed communications such as emails over the last two decades have really enhanced supply chain management, making it easier to manage effectively.
5 reasons why effective supply chain management is important
Aside from the obvious advantages of lower costs and a faster production and delivery cycle, there are multiple reasons as to why good supply chain management is a must for any manufacturing business.
1. An improved flow of products and materials means shorter wait times from suppliers and faster delivery to customers meaning less inventory being held and less cash tied up
2. Customer satisfaction is improved and therefore the opportunity for repeat business thus enabling a sustainable business relationship
3. Better financial flow – improve your cash flow with faster processing times and less silo processes
4. Reliable materials supply prevents lost production time
5. Minimise waste by only ordering what is required
So how can an ERP system improve your supply chain management?
A pre-requisite for successful supply chain management is having the right information at the right time. By integrating ERP and supply chain management, manufacturing businesses can achieve greater visibility of their operations and accurate data on which to base decisions. You could say that an ERP system oils the cogs and the wheels of a sophisticated supply chain!
Proactive planning and scheduling:
With an ERP system, planning and scheduling become a lot simpler and more process and data driven. Businesses can use information generated from their ERP system to decide in what order and priority they should run their orders and predict demand to ensure that the purchasing and production departments have the capacity to meet this demand. An ERP system allows senior managers in a manufacturing company to plan, manage and execute better and faster, whilst interpreting constantly changing information from customers and suppliers.
Improved purchasing:
With an ERP and supply chain management working together, your purchasing or procurement team will be able to take advantage of just-in-time and other purchasing methodologies. Purchasing can also be automated, with built-in triggers set to automatically place orders with suppliers when inventory levels fall below a certain level, amalgamate purchase orders for a common supplier, and change and update dates quickly on the fly. With improved visibility across all purchase orders and information on supplier lead times, inventory levels can be optimised, increasing cash flow and minimising fixed assets.
Supplier performance review:
Each supplier and their incoming deliveries will be in the ERP system in accordance with outstanding purchase orders and expected delivery dates. Any changes that take place, whether on the customer or supplier front, will be updated live in the system. ERP software can track the performance of your suppliers using metrics such as cost, delivery time, traceability, quality reports, etc. allowing you to negotiate better rates or to justify switching suppliers.
Increased automation:
Unnecessary tasks and approvals are not required. Employees can synchronise their activities in line with customer orders (whether firm or forecast), encourage collaboration and improve decision-making. As required, automatic or manual authorisations can be created based on the roles of the employees and workflows across all departments, which will enable increased business process automation in a manufacturing company.
Better decision making:
With real-time information, companies can manage and monitor their supply chain performance and analyse and quickly act on issues in sales orders, purchasing, replenishment of stock, incoming deliveries and shipments, customer orders, internal resource and capacity constraints. Manufacturing companies that implement a good ERP system are able to make decisions in a timely manner, mitigate risks, implement those decisions for completion of the products and facilitate fast growth.
Real-time KPI analysis:
Because the above information is integrated into the ERP system, it becomes much easier to track progress real-time against overall business objectives and enables companies to review processes and improve productivity and performance.
Improved information flow and communication:
All related documents and communications whether they are verbal, written or electronic can be stored and tracked in the ERP system – information is shared and flows much more quickly to all parts of the organisation. The ERP system facilitates the reduction of the duplication and allows every company in the supply chain to be measured on their individual performance, especially delivery and quality.
Better quality control, documentation and compliance:
For manufacturers who operate in sectors such as oil & gas, aerospace and nuclear, customers demand strict quality controls, creation of quality documentation and certificates for traceability and compliance purposes. Quality control processes can easily be planned, managed and executed in the ERP system. Necessary documentation can be created and tracked resulting in assurance and compliance internally and externally.
The integration of ERP and supply chain management will give your company a genuine competitive advantage within the industry and markets you operate in. By combining supplier pertinent financial data, inventory management and other key data into an ERP system and then sharing that information across relevant departments, your company will improve performance, efficiency and overall customer satisfaction.
If you’d like to find out more about how E-Max ERP can help improve the efficiency of your supply chain, take a look at our website, contact us on 0808 109 2035 or drop us an email. You can also book a free demo with us to see our manufacturing ERP system in action.