Using ERP software in project based manufacturing companies
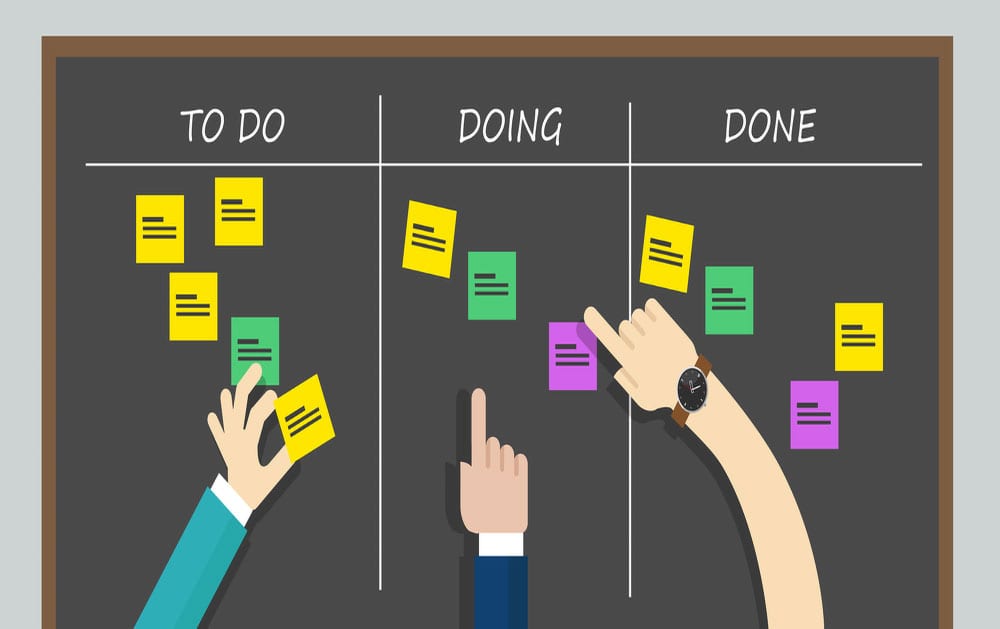
Manufacturing and engineering companies that engineer-to-order operate in a highly challenging and competitive environment. Often facing rapidly changing operational requirements as a result of their customers’ customers varying their requirements, manufacturers, and in particular, project based manufacturing companies, need to be able to accurately track and review every element of a job to ensure they remain profitable. In today’s blog, we’re looking at some of the ways using an ERP system can help manufacturing companies manage these complex projects, from the initial design right through to invoice.
Engineer-to-order manufacturing process
Unlike traditional manufacturers and engineers who make-to-order specified tried and tested items within a relatively short timeframe, companies involved in engineer-to-order projects often find themselves engaged in a complicated project over a much longer period. A number of our customers in industries such as mining, nuclear and oil and gas, are regularly tasked with developing a product concept, which generally involves many more stages than a traditional make-to-order job.
Let’s run through the stages of an engineer-to-order project. By the time it reaches the manufacturer or engineering company, the concept and operational requirements are most likely to have been determined. Drawings and support documents are available during the initial stages but several iterations might be required until the final design is released and accepted. Prototyping and testing will then take place, followed by final approval to commence manufacturing. Once completed, the output needs to be dispatched and commissioned.
The tasks and activities related to these initial phases, before any manufacturing takes place, all utilise resource and should therefore also be planned, managed, costed and charged to the customer according to project stages by percentage completed.
As a result, most manufacturing companies are constantly reviewing how they operate. To become more competitive they need to find new ways of working and adopting innovation to balance their operational processes against their customers’ requirements.
By adopting a project-based approach, including the need to manage increasing product complexities, change requests, engineering and design time, incorporating new technologies and software into the final assembly, etc. as well as the actual manufacturing timescales, the whole job can be planned and managed more efficiently.
ERP systems enhanced functionality
Over time, ERP systems, like E-Max ERP, have come to the party and offer project management functionality and features to enable companies to manage each project as an entity with work breakdown structures, activities and workload processes. With the use of effective project management for people and processes and incorporating appropriate software features like Gantt charts, scheduling, and capacity planning, the project can be visually simulated and supported. If a customer wishes to integrate or interface with an existing project management application, E-Max ERP has a feature to import the whole project schedule so that a customer’s project can be supported real-time and seamlessly.
Whilst managing the whole ‘design to delivery’ cycle as part of a single project is a typical situation for some of our customers, we are seeing an increase in companies who are increasingly having to manage multiple concurrent projects i.e. more than one project is carried out at the same time for multiple customers.
These projects inevitably vary in size, importance, required skills, and urgency. They can be in various stages of planning, execution and completion. Most importantly, they are using the same pool of resources available within the company in which departments undertake a number of duties through a project format.
Using an ERP system with project management enables projects to be planned with specific timelines and major milestones to be set. Required tasks, deadlines, responsible team resources can all be built in, with any shortages or issues easily identified.
Unlike in traditional use of an ERP (or even MRP) system, the actual manufacturing of the goods would be treated as a phase or stage of the overall project, as opposed to the whole project. This consists of all the usual cutting, welding, assembly, time and attendance, material flow, issuing material to a job, stock transfers, tests, certificates, etc. that you would expect to take place in the manufacturing of the item, but also allows for the earlier development phases of the project to be included as part of the job.
E-Max ERP helps companies overcome a major issue relevant to allocating resources to different projects and prioritisation among them i.e. project classification and categorisation. If projects can be grouped into categories, this makes prioritisation easier and simpler, and enables the introduction of organisational policies for contract review, project selection and approval. In a department with multiple small-size projects of varying ranges of importance, project priorities can shift on almost a daily basis.
After the initial phases of selection and approval, project categorisation and prioritisation, are complete, the managing and monitoring of operations and business wide tasks that are planned as part of the project can be coordinated and monitored. Additional ERP system features such as shop floor data capture, capacity planner and finite scheduler, give the project teams and members the ability to capture time and costs real-time and benefit from visual aids and tools.
ERP systems with project-based functionality and capability help companies put in place the required extensive interface with key departments such as development, engineering and the manufacturing areas involved in developing and designing new products. These systems also facilitate ongoing product support. Other potential benefits of using ERP in project based manufacturing include:
- Quick access to historical data for costs, quotes, and previous projects so that costs can be estimated quickly and easily during project bidding phase.
- Track and monitor project status real-time
- Track and monitor estimated and planned costs versus actual costs
- Just in time purchasing / procurement without the need for unnecessary inventory / stock
- Better cash flow management as percentage completion and earned value can be monitored at all times and the customer will be invoiced accordingly
- Personalised user screens or dashboards for project members in order to manage their tasks and project KPIs
- Post project support and service management if required by the customer.
Companies who utilise an ERP system in engineer-to-order projects will see clear benefits. Foremost of these are improvements in project planning and execution, and problem solving with an ERP system highlighting any areas that are at risk of running behind schedule or with resource implications. An ERP system will also provide clear visibility of all costs associated with the project, with every transaction and associated cost being charged to the project activities. With cost transparency, it is simple to see where processes need to be improved and developed. Cash to cash cycle improvements are also likely as each phase can be costed and invoiced separately. An ERP system will also control resource allocation and utilisation and enable quality improvements with every piece of material tracked throughout the project.
For more information on E-Max ERP and how it can help with your project based manufacturing requirements, take a look at our website, contact us on 0141 644 4424 or drop us an email. You can also book a free demo with us to see our manufacturing ERP system in action.