Why ERP Software for Small Machine Shops Gets Results
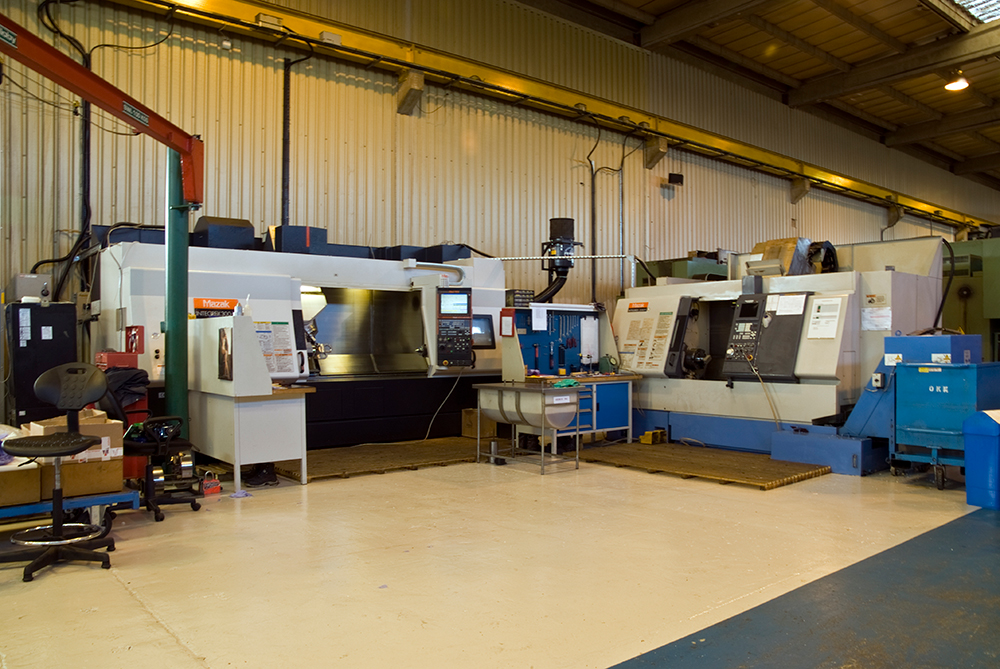
ERP systems may once have been the province of large corporates but we’re glad to say those days are long past, with thousands of small and medium sized firms adopting ERP to help them reduce costs, manage growth and increase their efficiency. Yet many smaller businesses, like machine shops or job shops, have concerns that their size will limit any real gains from an ERP system so dismiss the idea. In this post, we’ll address some of the concerns we hear and hopefully show that there are plenty of reasons as to why using ERP software in small machine shops brings real benefits.
1. An ERP system is way too complicated for us
Ok, you’ll need some level of computer literacy but most of the processes within an ERP system are very straightforward once learned. Go into the project with your eyes open and the expectation that you will need to set aside a few days for training and you’ll be pleasantly surprised as to how quickly you can be up and running. ERP developers work hard to make their systems as user-friendly and intuitive as possible.
A good ERP provider will work with you to help map out your processes so the system can be aligned to these. Most ERP consultants will have worked with other companies and have the knowledge and experience to guide you through the process. And if you think ERP is complicated, think about all the paperwork, spreadsheets and manual production calculations you’ve worked through over the years!
2. The cost is too high
This is probably the most common objection we hear and we understand. Especially today, as businesses fight to stay afloat. However, the goal of an ERP system is to make your business more efficient and productive and it’s not uncommon for smaller businesses to see a ROI within a year.
If cost is an issue, consider starting with a more entry level version of the software and adding in more functionality as you grow. This allows you to automate many of your business processes from day one, saving time, money and resource immediately.
And investigate what the costs of a system will be. We’ve come across far too many companies who truly believe that the costs of a fully functional manufacturing ERP system are out of their reach, only for them to discover the price tag was not nearly as high as expected for the functionality they wanted when they made enquiries.
(Note: now is a great time to be looking at funding support, with the Government and local authorities offering grants to help companies recover from the last few challenging years.)
3. Other Machine Shops get by without ERP software
But many more are adopting it. Don’t get left behind by your competitors as they respond to RFQs faster and more accurately than you. Use the information your ERP system provides to work out a fair profitable price for yourself whilst remaining competitive in the marketplace. You’ll be able to see the true costs of every job and know what you need to make on new jobs to breakeven and profit. You’ll also be able to identify spare capacity and make use of it, reducing downtime and running more jobs.
4. ERP is just an expensive accounts system
It’s true that an ERP system can manage your accounting processes but it can do a lot more than that. Because an ERP system connects all areas of your business, from inventory, shipping, production (including raw material, labour and machine time), it gives a true picture of what’s going on. This allows you to identify where you are making money (or not), what’s being under-utilised, wastage, etc – valuable indicators that enable you to make informed decisions about your business. You won’t get that depth of information from accounting software.
Many smaller businesses already use accounts software like Sage, Quickbooks or Xero and are reluctant to disrupt the status quo. Most ERP systems allow you to connect to these products so you can benefit from the richer information integrated ERP and accounts provides.
5. We’re too small to need an ERP system
The thing about manufacturing, especially make to order or small batch manufacturing, is that all companies, large and small, go through the same complicated processes. Whatever size of company you are, you still need to quote, purchase, manufacture, quality check and deliver the final product – the main differences being that smaller companies tend to be more stretched resource-wise and have less ability to absorb errors. Using an ERP system to schedule all your resources, from machinery to materials to labour, enables you to optimise your performance and get more done, with less. An ERP system allows you to standardise your processes, which in turn reduces costly errors.
So if you think that your manufacturing business is too small to afford or use an ERP system, then maybe it’s time to think again. We hope we’ve covered enough reasons as to why ERP software for small machine shops is a great way to strengthen and grow your business but if you’d like to find out more, why not have a chat with one of our experienced ERP consultants on 0808 109 2035?
If you’re interested in finding out more about how E-Max ERP, our ERP solution for SMB manufacturers and engineers, can make your business more efficient and profitable, then please visit our website or request a no obligation demonstration to see E-Max ERP in action.