7 Ways to improve your shop floor scheduling
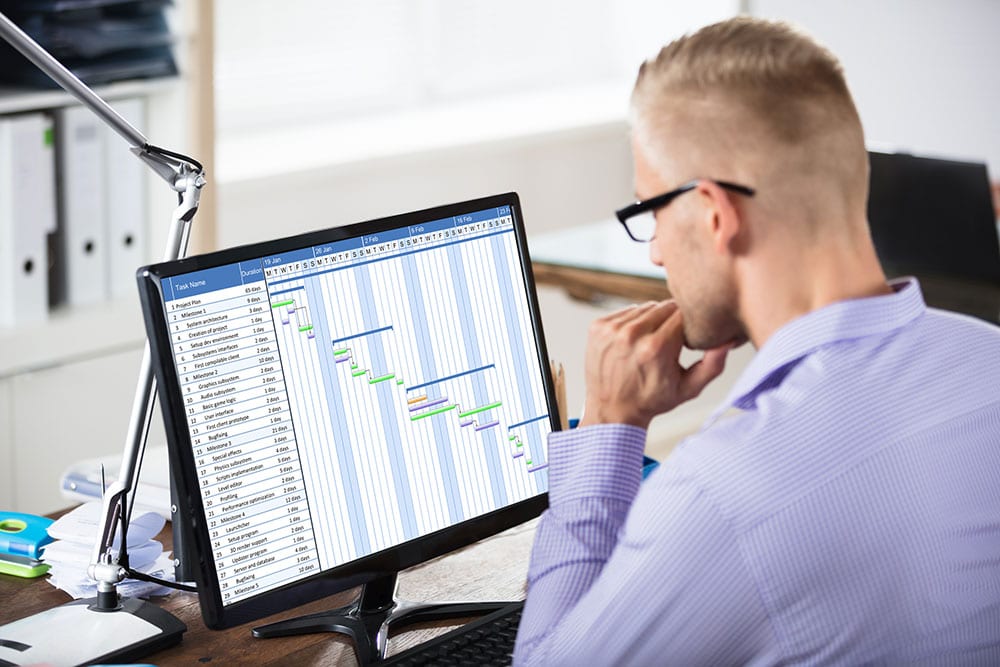
Consistent on time delivery to your customers is a necessity in today’s fiercely competitive manufacturing world. If you can’t achieve this, your customers will look elsewhere. We all know there’s many reasons jobs run late – a delayed delivery of raw materials, changes to jobs, the (in)availability of workcentres and operators, and the inevitable ‘rush’ jobs that need priority, to name a few. And then, as more jobs run late, quality suffers as you rush to get them out the door. Keeping to a planned schedule can be nigh on impossible. However, there are some actions you can take to improve your shop floor scheduling and keep your customers happy.
1. Quote accurately from the start
The longer you take to respond to an enquiry, and every revision of a quote you do thereafter, eats into your production time. Try to simplify your quoting process as much as possible. Estimating these jobs can take time in an OEM or MTO environment as the majority of these jobs won’t follow a standard routing. There will be some guesswork involved but if you can use previous jobs as a basis (especially if these are stored in a system) you should be able to create a reasonably accurate quote. Make sure these quotes are included in a production schedule and updated regularly to minimise surprises on the shop floor.
2. Know your inventory
Managing your inventory effectively is a key factor in improving your shop floor scheduling. You need to have the raw materials available at the right time to start your jobs but at the same time you don’t want to back up your stores (or your cash flow) with excessive amounts of inventory. If you know what inventory you need and when it’s due to arrive, your shop floor schedule will be much more accurate.
3. Recognise your capacity
Do you know the maximum your shop floor can handle? Are you constantly adding jobs to the shop floor and hoping that you can accommodate them? Disregarding the constraints of your shop floor (labour, machines, tools, etc) will lead to optimistic and unrealistic delivery dates. Applying finite rules (ie only one person can work on one operation at a time) will give a much truer picture of what can and can’t be achieved within specific timeframes.
4. Group similar jobs
It’s difficult to identify similar jobs if you have hundreds, even thousands, of works orders on the go but the effort is worth it. You’ll reduce set up times and material handling, which frees up resource that can be utilised elsewhere.
5. Make sure your data is real time
And update your plan regularly with this live data. If you are relying on out-of-date information, then you’ll never get your scheduling issues resolved, whereas making decisions based on real time data will really help improve your shop floor scheduling. Get buy-in from your workforce, making sure they regularly update activity progress. If you are using Shop Floor Data Capture (SFDC), don’t skimp on terminals on the shop floor – people are much more likely to comply with a system if they don’t have to walk halfway across the shop floor every time they need to log a task.
6. Understand the implications of changes to your production schedule
Let’s face it, you’re never going to be able to completely avoid taking on rush jobs. Whether it’s a favour granted by the MD or a last-minute order from a preferred customer, rush jobs will always arise. But if you understand what the implications of making these changes to your schedule are, and what these mean to your business, you can readjust your schedule to minimise the impact this has on other jobs.
7. Automate your scheduling
Probably the best way to improve your shop floor scheduling is to invest in scheduling software, and, for maximum effect, link that to a wider ERP system. All information pertaining to every order is recorded and that data is used to calculate the most efficient scheduling of your shop floor, based on required delivery dates. Using scheduling software enables you take the guesswork out of the scheduling process and gives you a clear view of the outcome – ie if you make changes to the schedule, get a new revision for an existing job or accept a new rush job.
There’s no doubt that scheduling is a notoriously difficult aspect of manufacturing and whilst there’s no magic bullet for it, applying some or all of the above ideas to your scheduling process will give you better results and improve your on-time delivery to customers.
If you’d like more information on E-Max ERP and our scheduling functionality, take a look at our website, give us a call now on 0808 109 2035, email us or arrange a short personalised online demo to see how E-Max ERP can truly improve your shop floor scheduling (and so much more!)
Enjoy this post? Check out our other blogs like Rough cut performance improves delivery on time performance or Get a real time view of your shop floor with SFDC