The Importance of Material Requirements Planning (MRP) in Manufacturing
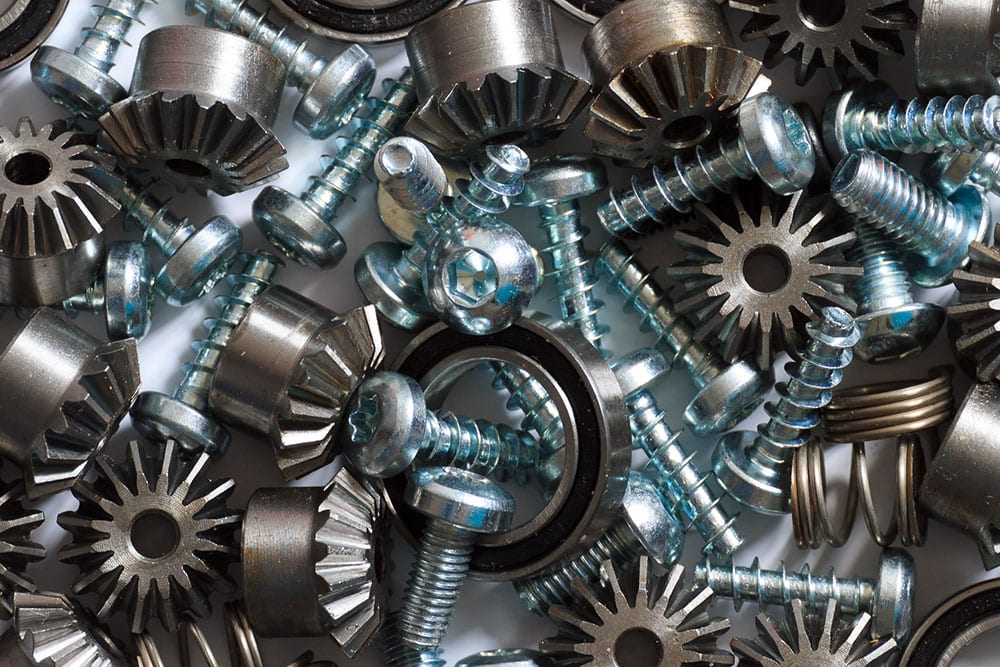
In this week’s blog, we’re going back to basics with MRP and why materials requirements planning is so important in manufacturing.
Materials Requirements Planning (MRP) was developed back in the 1970s to help manufacturers streamline their planning, production and inventory control. It is a framework to help businesses plan operations, control their inventory and organise their logistics. Done properly, MRP ensures that manufacturers have the right quantity of materials at the right time for production to take place.
Managing this flow of raw materials, components or parts from their supply chain and into production and onto the customer effectively is challenging but necessary for the continued success of every manufacturer. Poor management of these means there’s a very real possibility that you’ll either run out of inventory or be unable to fulfil your customer orders. In today’s highly competitive environment, these are not risks any manufacturer wants to take.
Material Requirement Planning (MRP) in Manufacturing
In order to calculate what material is required and when an order can go into production, an MRP system takes into account information on current and future orders, forecast demand, the master production schedule, the Bill of Materials (BOM) and inventory.
An MRP system will allocate or reserve the stock it needs from your inventory, then raise purchase orders for any outstanding materials required. It will factor in timescales for the delivery of these items and calculates when production needs to start to meet the customer’s required delivery date. The MRP then generates the work orders and can provide reports on the above.
MRP can be used for both Make-To-Stock and Make-To-Order manufacturing. Companies who Make-To-Stock are more likely to see the immediate benefits of material requirements planning but those companies who Make- or Engineer-To-Order can also benefit from using an MRP system in areas like scheduling, purchasing, inventory control and labour management. Some MRP systems, like E-Max’s, offer specific functionality for ETO manufacturers including customisable BOMs and modifiable routing.
Benefits of Materials Requirements Planning (MRP) in Manufacturing
The main benefits of materials requirement planning are:
Better inventory control – minimise the amount of inventory you are holding whilst keeping production on track. Using an MRP system means that you can avoid holding rarely used or excess materials for long periods of time whilst remaining confident that you won’t have any shortages of key materials.
Reduced costs – both for you and your customers. By holding less stock, you have less working capital tied up. With fewer raw materials or components held in stock, you can reduce your storage costs. These cost savings can be passed onto the customer in the form of more competitive pricing.
Improved scheduling – MRP gives a clear indication of when production operations need to be carried out. This enables your production managers to see what labour they need and when and avoid expensive overtime.
Excellent customer service – utilising MRP enables you to deliver in full on time to your customers
Production Planning – production of the end product (or even sub-assemblies of a complex project) is dependent on the availability of the raw materials or components. MRP highlights any shortages so that your production manager can reallocate your work centres, machinery or labour for alternative jobs that have a complete inventory.
Problems with using Material Requirements Planning (MRP) in Manufacturing
Whilst there can be a few issues around using an MRP system in manufacturing, most MRP systems are proven to offer significantly more benefits than spreadsheets or manual calculations. The main concern around MRP is generally data quality.
A system is only as good as the data entered into it and data that is not kept up to date or contains errors will give inaccurate results. Mistakes often arise during cycle-count adjustments, data entry and shipping stages or reporting of scrap, damage or waste. Using barcode scanners and daily recording of scrap, damage or waste is one way of minimising these errors but another is to use an MRP system as part of a wider ERP system.
By integrating your MRP with ERP software, all your data is held within one system and is easier to keep up to date and accurate. Your quotes estimates and orders will be combined with inventory and production so it’s simple to raise sales orders whilst checking you have access to the right materials and ensuring you have the capacity to fulfil an order in the time required.
Conclusion
Using an MRP system simplifies the complex and time-consuming operation that is materials requirement planning and enables businesses to better manage orders and organise their materials. Whilst some small to medium sized manufacturers continue to do their materials requirement planning manually with spreadsheets, most manufacturers are adopting MRP systems (either standalone or integrated within ERP systems), finding that it saves time, gives structure to their planning process and eliminates errors. Having an MRP system in place allows manufacturers to keep up with increasing demand and become more streamlined and efficient in many of their processes.
E-Max ERP is a fully functional ERP system, developed by engineers and in consultation with our manufacturing customers. At the core of E-Max ERP sits a powerful MRP system, which means you can benefit from all the above. If you’d like to find out more about E-Max ERP, then take a look at our website, contact us on 0141 644 4424 or drop us an email. You can also have a free demo with us to see our software in action.
If you’ve enjoyed this article, why not register to receive our monthly update on the latest industry and ERP trends. Over the coming weeks, we’ll be looking at topics like using ERP for ISO accreditation and whether ERP is the new crystal ball?