Choosing a Shop Floor Data Collection system (SFDC) for Manufacturing
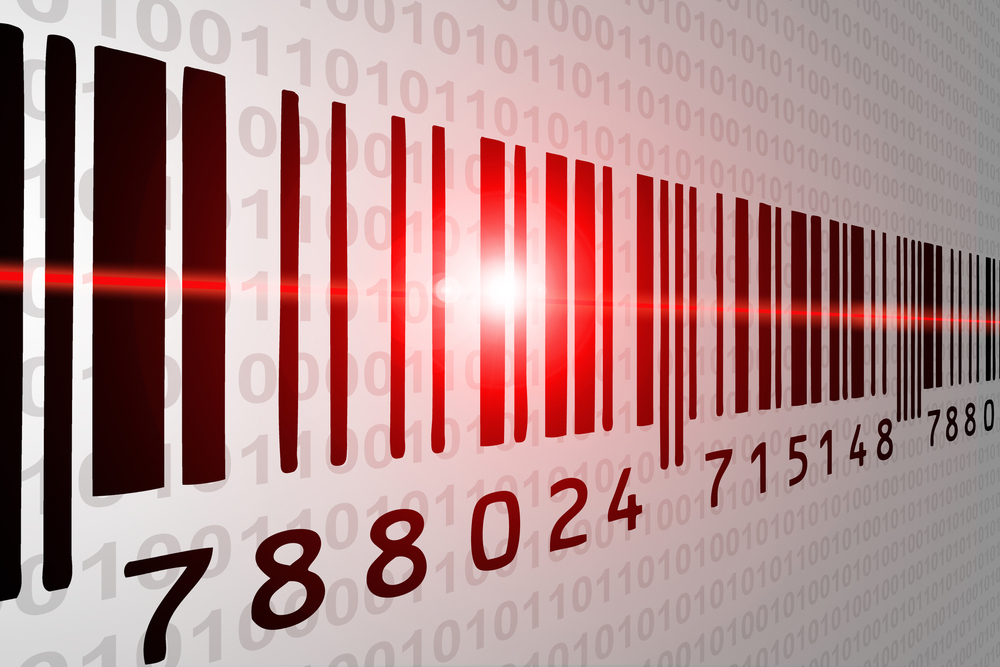
A quality shop floor data collection (SFDC) system can bring significant benefits to any manufacturing or engineering business. It’s no surprise then that an increasing number of companies are investing in an SFDC to reduce time, effort and costs on the shop floor. However, not all data capture systems are created equally so let’s take a look at what you should be looking for when choosing a shop floor data collection system.
1. Does it integrate with your existing systems, in particular your ERP or MRP system?
SFDC gets best results when integrated with an ERP or MRP system – there’s no doubt about that. By feeding the information you collect from your shop floor into your company wide system, you can easily analyse that data. If the data from your SFDC can’t flow straight into your legacy systems, ie if you need to export it from your SFDC and then import into spreadsheets or other analysis software, then it can’t do the job to best effect. Time delays in processing this information mean slower, not better, decision making.
Information should also be able to flow two ways – if your ERP or MRP system can send data to your terminals on the shop floor, machinists can reference useful information such as next job, instructions and specifications, without having to break from their work routine.
2. How easy is it for your team to use?
A key objective of an SFDC is to capture information on costs and efficiency so the last thing you want is to add time and effort to this process! A good SFDC needs to be easy to use, with a simple user interface designed to remove any ambiguity and ensure that the data collected is accurate. E-Max’s SFDC offers a variety of simple data capture options, ranging from barcode or fingerprint scanning to RFID or smart cards.
Speed of use is also important to consider when choosing a shop floor data collection system. There’s very little point in bringing on a system to improve production efficiency if it takes operators an extra 5 minutes every time they need to cross the shop floor to log their task in a terminal. It’s often much more cost effective to add more terminals on the floor and reduce the time spent away from the job from minutes to seconds. Taking this a step further, machine dedicated terminals (ie a terminal at every machine or work centre) bring big advantages in ending operator travel time, reducing data entry (machine is already known so no need to input that information) and enables the operator to see their upcoming tasks.
3. What are the costs and ease of implementation?
The bad news is that adding machine dedicated terminals is likely to increase the cost of an overall SFDC system. However, the good news is these costs are mitigated by the increase in efficiency enabled by close proximity of the terminals and the decreasing cost of hardware like scanners and terminals (often less than £300 per machine or work centre). These additional costs are generally recovered within a year or two of implementation.
The cost of the actual SFDC software will vary across individual vendors but one area that should be considered is whether there is a requirement to use the provider’s proprietary equipment or hardware, such as specific scanners, barcode readers or keypads. If this is the case, consider the cost of the whole setup as using such proprietary equipment can over-inflate costs. There can also be issues sourcing very specific equipment, especially if it comes from overseas, with longer lead times and therefore potentially longer downtime in the case of broken or damaged equipment. Industry standard equipment, such as E-Max would recommend for anyone choosing a shop floor data collection system, can generally be sourced quickly and cost effectively, thus minimising these risks and making initial implementation easier.
Also worth reviewing is how easy an SFDC is to implement. If an SFDC system needs to connect to multiple legacy systems, ie production, inventory, accounts, etc, currently in use within your company, the implementation period is likely to take much longer and cost more. If, however, you are interfacing your SFDC with just one software system that encompasses these functions, such as an ERP system, implementation becomes a much more straightforward and immediate process. When choosing a shop floor data collection system, it’s imperative you consider whether it is configurable and flexible enough to meet your shop floor needs.
4. Does it have the functionality to meet my requirements now and in the future?
At present, all you may want your SFDC to do is accurately measure the hours worked on specific jobs. You’ll save hours of time in data entry, avoid manual errors and stop duplication. You’ll get information on job costing immediately, at the touch of a button, allowing you to see whether a job is going over budget and have the ability to take action when it counts, not days later.
However, what if in future you might want more functionality? Consider:
– Does your SFDC offer Time & Attendance as well as just Time Bookings?
– Does it allow machinists to clock onto multiple jobs concurrently?
– Can you split an operator’s time across jobs?
– Are Supervisor Screens available so a supervisor has a full picture of what’s happening now?
– Can your SFDC provide operators with additional information to help them in their job – ie store drawings, specifications, instructions?
– Does it issue material to a job to get more comprehensive costings?
These are just some features a quality SFDC should offer but often these systems only capture the bare minimum. E-Max’s SFDC offers the above functionality and more – ensuring that you have the capabilities you need from your SFDC. The more knowledge you have, the better the decisions you can make. And of course, if you don’t need all of the above information now but may want it in future, we can keep things simple by setting the SFDC up to only use the features you need today.
In order to stay competitive and profitable, manufacturers today use continuous improvement methods to try to achieve optimal production results based on machines, equipment and processes used. Monitoring of shop floor activity is a big part of this and so it is vital that data collected from the shop floor is accurate, timely and available to the business’s decision makers so that they can continually monitor production and make improvements. At E-Max, we firmly believe that by asking the above questions when choosing a shop floor data collection system and then implementing the resulting quality SFDC, manufacturers can be confident they have the tools in place to achieve necessary improvements.
To find out more about E-Max’s Shop Floor Data Collection and how we can help you increase efficiency across your business, take a look at our website, contact us on 0808 109 2035 or drop us an email. You can also book a free demo with us to see our manufacturing ERP system in action.