Identify & eliminate bottlenecks in manufacturing
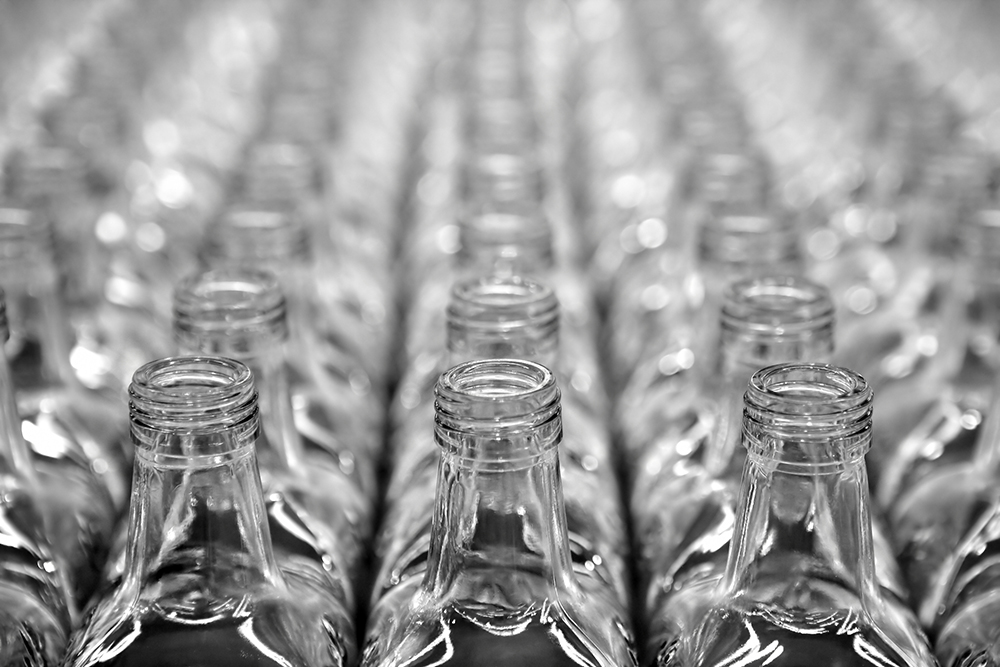
Process bottlenecks in manufacturing are virtually inevitable yet left unresolved they can really impact your company’s ability to deliver your orders on time, incur additional costs, and restrict your company’s growth. However, it’s generally not the bottleneck itself that is the real problem – it’s merely the warning sign that highlights a deeper rooted issue is at play. To identify the real issue, you firstly need to firstly identify the bottleneck, then work backwards to work out what’s causing it and develop a solution to that problem. Below are a few ways to help you identify and eliminate manufacturing bottlenecks to keep your processes running smoothly.
What is a bottleneck?
A process bottleneck is essentially a stage in your operations that receives more requests than it can process. This causes delays in subsequent processes and limits your entire capacity so it’s no wonder the removal of these should be a priority.
There are two main types of manufacturing bottleneck – short term and long term.
A short term bottleneck is a temporary issue that can often be resolved quickly but, depending on when they occur, can have mild to significant repercussions. Typical examples of this include a machine breaking down or requiring maintenance; employee absence through holiday or illness; or a supplier delivering late. Using an ERP system can help mitigate the impact of these – scheduling will highlight upcoming employee absence or machine maintenance, whilst inventory management can anticipate and act on shortages.
A long term bottleneck is a very different matter and can bring your production floor to a standstill. These tend to be a persistent problem, causing regular interruptions or delays to the production process. Examples of these could be an inefficient machine that causes a long queue to build up, extended downtime on the production floor due to long lead items, delays converting designs to the MRP stage or a build up of items for jobs in process.
Bottlenecks in manufacturing put huge pressures on a production department, causing backlogs and meaning the team is in a state of constant flux as they try to get the most urgent orders out on time. To get your operations running smoothly, you need to identify and resolve these bottlenecks.
Identifying a manufacturing bottleneck
You know things aren’t working as well as they could be – there are machines and operators idle on the shop floor, yet orders aren’t going out when they should be. Here’s 5 ways to identify bottlenecks:
#1 Map out your processes
We meet lots of companies who haven’t fully mapped out their processes and understandably so – it can be a time-consuming activity. However, the benefits of analysing your processes and determining whether they are truly logical and methodical (not hastily conceived workarounds!) are significant, so it’s worth investing the time and effort. Not only will it allow you to identify bottlenecks, it gives you the opportunity to implement more efficient and effective processes.
#2 Examine your capacity
Tracking the percentage utilisation of each machine, work centre and resource within your business will help you identify a manufacturing bottleneck. The machines or resources (which can include personnel with specific key skills – ie welding, etc) with the largest percentage will most likely be your bottleneck. Other machines, centres and personnel will have lower percentages as they are constrained by the bottleneck. Increasing capacity where the bottleneck exists can increase the capacity of the whole production floor.
#3 Review wait times
If you are not tracking capacity utilisation, an easier way to identify bottlenecks is simply to look at the downtime of machines or personnel. The step preceding the machine or work centre with the highest downtime (or wait time) is your bottleneck.
#4 Question queues
Are queues regularly occurring in the same point of production? What is causing this? This could be due to an inefficient work centre, slow worker, or regular machine breakdown – either way, once you have identified the problem, you can now resolve it.
#5 Adjust your throughput
If the above haven’t thrown up any key findings, you may need to adjust the throughput of each individual area on your production floor. The area that affects the overall output the most is your bottleneck.
Eliminating bottlenecks in manufacturing
You’ve identified the bottlenecks, worked out the root cause and developed a solution. So how do you prevent others? That’s the £64 million question! Much as we’d like to say otherwise, it’s probably not going to be possible to eliminate every bottleneck in the manufacturing process. However, knowing the areas where you are weakest is valuable. It means you can reprioritise activities around these areas and work to achieve maximum capacity across all your machines and resources. And once this is done, you’ll need to keep reviewing your processes as new bottlenecks will arise. Identifying and eliminating bottlenecks should be considered to be an ongoing continuous improvement process, but one that will enable your company to prosper.
The good news is that using an ERP system to identify and resolve these manufacturing bottlenecks will most certainly help. For example, an ERP system will:
- schedule machine maintenance to occur at the least disruptive times
- manage inventory and highlight shortages
- provide real time alerts as problems arise
- collect and analyse data to measure and report on performance of every area, including machines, work centres and personnel
- identify drops in productivity and quality
- flow information electronically across every department, removing delays in paper transfer
and enable your operations to run smoothly and efficiently.
Find out more about how E-Max ERP can minimise the impact of manufacturing bottlenecks on your business and help your bottom line. Speak to our team directly on 0808 109 2035, message us today or take a look through our website. If you’d like to see E-Max ERP in action, one of our specialists can take you through a no obligation demo.