Rough cut capacity planning improves delivery on time performance
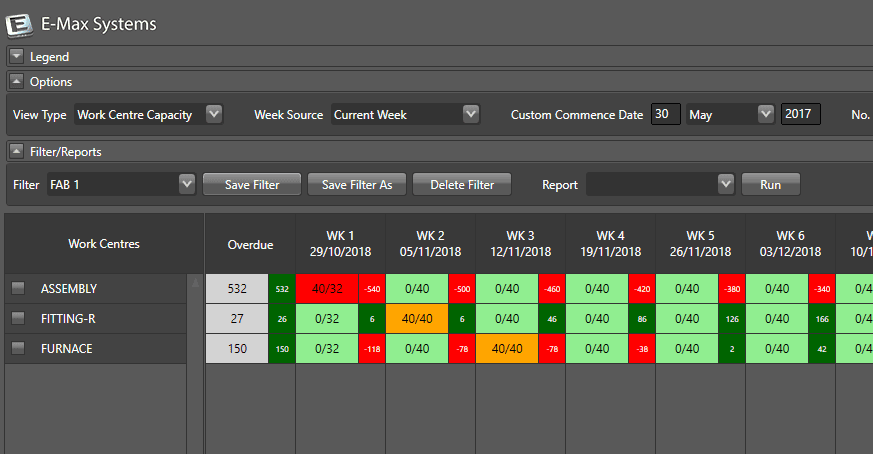
Every manufacturing and engineering company uses some form of a master production schedule to plan in their daily, weekly and monthly operations. It’s imperative that the production of jobs is planned in to avoid orders being late or even forgotten but what a master production schedule won’t show the management team is whether the business has the capacity to execute that schedule. This is where rough cut capacity planning becomes a vital part of the planning mix.
What is Rough Cut Capacity Planning?
In its simplest form, rough cut capacity planning (RCCP) allows your business to calculate whether it has sufficient capacity available to meet the capacity requirements for your master production schedule. RCCP is a long term planning tool that Sales, Marketing and Production departments use to balance the required and available production capacity and use this information to adjust their master production schedule.
Rough cut capacity planning focuses specifically on capacity, which can be altered by adding or removing machines or workcentres, by using overtime or even subcontracted labour, or by adding or removing shifts. What it doesn’t factor in is your current inventory, assuming that you will have the required materials to produce the job. By integrating your RCCP with your ERP system, inventory information can be reviewed in conjunction with the master production schedule, allowing you to generate precise MRP plans.
When to use Rough Cut Capacity Planning
RCCP is an ideal approach to scheduling where:
- The production processes of product can’t be fully described by the route entered into the system due to the complexity of defining each task in the process – eg typically in the case of a prototype or new fabrication
- The routes don’t contain enough information on the order of the tasks in the manufacturing processes and the implications of these – eg there is no interop time in the route to move material from one operation to the next
In the above scenarios, the following actions need to be undertaken so the rough cut capacity planner can understand what time values are attached to each task
- Recording the expected time for each process in a job in its route records
- On the assumption that each component in the assembly has a linear production route, the RCCP then works out, from the delivery date of the works order, the last start date of each operation
- If the product is an assembly as opposed to a flat item, the RCCP starts from the final assembly, works out the start date of its works order, goes to the next level and does the same and so on through the whole bill of materials (BOM)
- For that complete job one ends up with a number of operations across every level of the BOM, each with their own last-start dates
- If an item in a job does not have a linear route but the planner still records the time for each operation, one can intervene and manually override the start dates
- A lead time can also be used to calculate the start dates of the works order within a BOM
Benefits of using RCCP
So we end up with this list of operations for all outstanding job operations. What advantages does this provide manufacturers and engineers?
- We can use this list to improve project management ie we can identify operations that should have been started by a specific date – late operations
- Allows the production team to prioritise operations by start date
- We can total by week the number of hours of work we have to do by process eg machining dept, or by work centre or even by person to identify if there is too much or too little work there and adjust capacity accordingly through the number of shifts, workcentres in operation, etc
- The system will again by process or work centre show the cumulative outstanding hours by week. Thus, if a work centre has 20 hours work for next week and 60 hours for the week after and the capacity per week is 40 then at the end of the second week the expected cumulative outstanding hours is 0 (20 plus 60 less 40 x2=0). Had the load been 60 hours the first week and 20 the second management can see that at the end of the second week the load and capacity are equal but some operations which should have been started in week 1 need now to be done in week 2. By being able to view all the operations in a week one can identify operations that absolutely have to be done and ones that can slip.
The key benefit of using a rough cut capacity planner lies in the ability of an organisation to improve its delivery on time performance. With the transparency and knowledge provided by the RCCP, management are able to identify any areas of concern and take remedial action to ensure delivery on time targets are achieved every time.
E-Max’s rough-cut capacity planner
A graphical capacity planner like ours shows by work centre or process, by week into the future:
- Late operations ie what operations on jobs should have been done by today and the total hours required
- The total hours that must be completed each week against the available hours for that works centre or process
- The available hours will also be shown allowing the comparison of planned v available hours to identify bottle-necks
You can see this in the detail of our rough-cut scheduler below:
The overdue hours at a work centre, the capacity hours per week, the loaded hours per week and the cumulative hours can all be seen quite clearly.
Critically, this will also show when that work centre will run out of work. This is a potentially key piece of information for the sales and marketing functions to drive further business.
It is also simple to drill down into the balance for a week and see the list of jobs.
Handling bottle-necks
Planners can respond to bottle-necks in a number of ways:
- Operations can be moved from machine to machine if that is possible
- Overtime can be planned in for weeks where there is too much work in a particular centre or process. Also the production department can identify the work centre that needs the overtime, removing the need to put the entire factory on overtime
- By changing delivery dates, jobs can be moved forward in the schedule and re-scheduled which will move all their operation into later weeks
- Excessive or capacity consuming operations can be sub contracted in times of need
Rough cut capacity planning is an excellent methodology for controlling work going through a factory or job shop. RCCP, and in particular E-Max’s feature-rich RCCP, gives management great flexibility without minimal amounts of data input, and the benefits, in particular the ability to improve delivery on time performance mean it is an invaluable tool for any busy manufacturing or engineering business.
To find out more about E-Max’s rough cut capacity planner and how it can help your business, take a look at our website, contact us on 0808 109 2035 or drop us an email. You can also book a free demo with us to see our manufacturing ERP system in action.
If you’ve enjoyed this article, why not register to receive our monthly update on the latest industry and ERP trends.