ERP or MRP – Understanding what the differences mean for manufacturers
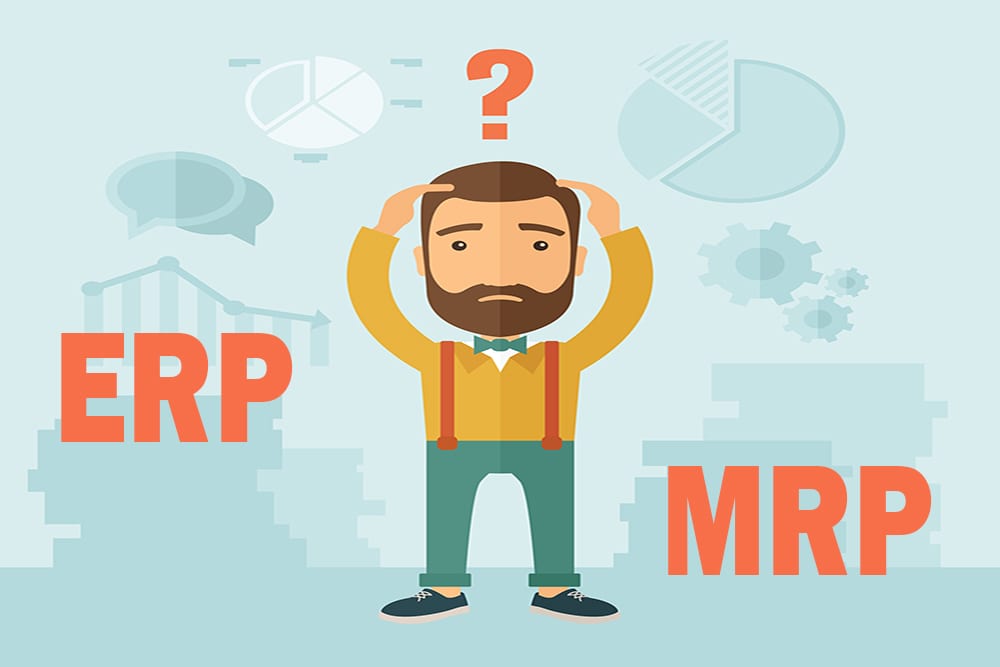
“What is the difference between ERP and MRP? Which one do we need?” are questions we’re often asked by companies looking to update the way they work. There’s a huge amount of information online about both ERP and MRP and their capabilities – so much so that the information can seem overwhelming. In this blog, we’ve summarised the key elements of ERP and MRP and what these offer manufacturing businesses looking for a new system.
Definitions of ERP and MRP
MRP (material requirements planning) is the original, most basic system and deals primarily with working out what materials and parts are required to manufacture a product. In its simplest form, an MRP takes information from a bill of materials (BOM) and the actions (or route) needed to produce the item. This information is then used to take inventory of the materials on hand, identify any additional required materials and then schedule the production of the job. In short, MRP is focused around inventory management, production planning, and scheduling and uses both actual and forecast orders to determine what items should be produced.
MRP II (manufacturing resource planning) goes a step further and includes some broader functionality, although this is generally still very much focused around managing materials and the manufacturing process. Basic accounting capabilities, capacity planning, quality control, shop floor data collection and inventory control have been incorporated into most current MRP systems and provide companies with much more detailed information than their predecessors. Sometimes known as a closed-loop system, MRP II solutions can provide feedback on given operations.
Although these systems are technically MRP II, they are now generally defined as MRP systems. The main objectives of an MRP system are to:
• Ensure the materials are ready for production
• Keep the lowest possible material and product levels in store
• Plan all manufacturing activities, delivery schedules and purchasing
• Ensure products are available for delivery to customers (on time in full)
ERP (enterprise resource planning) takes a whole-of-business approach as opposed to a purely manufacturing focus. ERP systems incorporate all of the above capabilities but also integrate multiple other functions into the same system, usually:
- Customer Relationship Management (CRM) – including quotes, estimates, contact management,
- Order Processing – sales orders, purchase orders, works orders,
- Financials – accounts including general, sales and purchase ledgers
- Quality Management – non-conformance, CofC, test reports
- Human Resources (HR) – training, absence and leave recording, shift patterns, time & attendance
- Warehousing & Logistics (distribution) – deliveries, shipments, materials traceability
In the last few years there has been a trend to increase the functionality within ERP systems, with some systems now incorporating product life-cycle management, project management and asset tracking capabilities.
ERP or MRP – what’s right for manufacturers?
Originally, ERP systems were predominantly developed for huge multi-national businesses. The costs of these mammoth systems were generally very high, implementation was also costly and very time-consuming and utilised valuable resource that could be allocated elsewhere in the business. But, fortunately, ERP systems have evolved, costs have reduced significantly and implementations have become faster and more efficient, making ERP systems both a viable option and valuable tool for small to medium sized manufacturers.
A standalone MRP system?
A comprehensive MRP system may well be enough for some manufacturing businesses. Provided key functionality is included within the system, manufacturers have access to information about materials, production scheduling, delivery forecasts, capacity, quality control and shop floor data. This enables them to capture production costs and make informed decisions around their materials and manufacturing process. However, because an MRP system is a standalone application, other valuable data is not integrated into it which may mean some decisions are not based on real time data. Examples of this include:
- An MRP system takes current and forecast orders to calculate what is required. If your CRM (containing forecast and actual orders) is not connected, information in the MRP may already be out of date and increases potential for errors
- Without warehousing, logistics and distribution integrated into the MRP’s inventory, future inventory levels cannot be predicted accurately
Or an integrated ERP?
The biggest benefit of an ERP system to a manufacturer is the integration across all departments. Instead of maintaining multiple different software applications across different functions, ERP brings these functions together so information is entered in once and flows through the business, from quotation or estimate, to sales order processing, through to production (where it is MRP-ed!), from then to purchasing and/or warehousing, back to production and scheduling, and finally through to delivery and invoicing (finance). Phew!
There’s no double data entry or communication issues with an ERP system, which all but removes the chances of manual error, forgotten stock ordering, or using out of date data. Other benefits of an ERP system to manufacturers include:
- Some resources, machines or workcentres may have a secondary constraint – ie they need an operator or skilled employee. By integrating HR with MRP, secondary constraints can also be factored in and managed. Downtime is reduced or avoided altogether when leave and absence data is synced to resource scheduling.
- The supply chain runs more smoothly as purchasing becomes semi-automated. Shortages identified by MRP can be procured with a single click or re-order levels can be automated.
Costs of ERP and MRP
The budget available for the new ERP or MRP system is usually a major factor in the decision-making process. Whilst ERP systems are usually more costly (due to the additional functionality included) companies should also assess what they are paying for other software such as accounts, warehousing or CRM packages. Comparing prices across various vendors is always advised as an ERP system designed for SMEs may be more cost effective than an MRP system designed with a corporate manufacturer in mind. If budget constraints mean an ERP system is unattainable, look carefully for MRP options that are already proven to interface with existing applications so certain levels of integration can be achieved.
ERP or MRP – let us help you decide what’s right for your manufacturing business
At E-Max, we are seeing more and more manufacturing companies now looking for a fully integrated manufacturing system that removes duplication and chance of error. In this age of Industry 4.0 and frictionless manufacturing, using a single system to help manage all business processes is a massive time and money saver. Increasing connectivity throughout the manufacturing process speeds up delivery time, removes errors, improves quality and reduces manufacturing cost thus increasing profit.
E-Max Systems began developing MRP software in 1997. Each of our original products were pure MRP systems so you can be confident that our software consistently includes a sophisticated and functional MRP system at its core. We’ve added functionality over time to develop these original MRP systems into a comprehensive ERP system, designed specifically for manufacturers and engineers.
However, we also offer options to companies who only want to take advantage of our MRP functionality. If, for whatever reason, you’d like to keep your existing applications but harness the power of our MRP system, the good news is you can. Unlike many other ERP or MRP software vendors, who only offer ERP or MRP systems, we’re committed to providing our customers with what suits them best so we’ve designed E-Max to integrate with multiple 3rd party packages, including Xero, Sage, Quickbooks, etc.
If you’d like to find out more about the differences between our ERP and MRP systems, and how it can help your business, take a look at our website, contact us on 0808 109 2035 or drop us an email. You can also book a free demo with us to see our software in action.
If you’ve enjoyed this article, why not register to receive our monthly update on the latest industry and ERP trends.