Using ERP for improved Quality Management
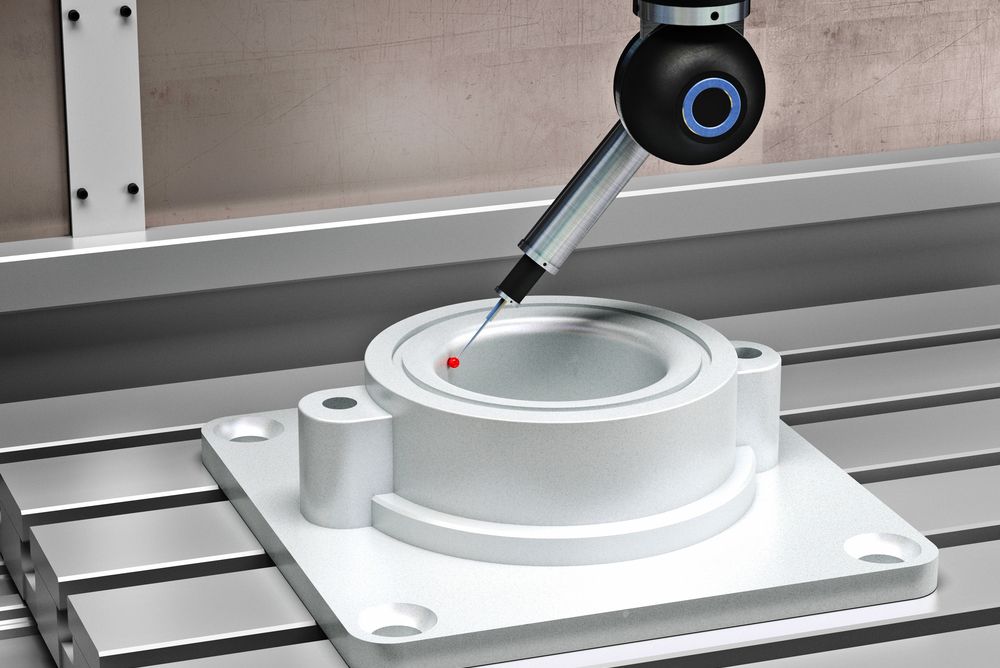
An effective quality management system (QMS) is a must for every manufacturing business. Fact.
Many of our customers operate in highly regulated industries such as oil and gas, aerospace and automotive, where a sub quality part could be the difference between life or death. Other businesses operate in less regulated environments but a common factor across all manufacturing and engineering companies is the need to assess and measure the quality of the items they are producing. Poor quality items mean loss of customers, reputation and added expense – factors that will quickly cause a business to fail.
E-Max ERP includes a comprehensive quality management system, designed with manufacturers and engineers in mind. Here we review how E-Max simplifies and streamlines the procedures and checks that a typical organisation needs to carry out to make sure its products meet the quality standards required. These standards can either be set wholly, or in part, by the government, the customer or the market.
Documents and Drawings
Most manufactured items have some form of document, whether this is a plan, drawing, or specification, that contains instructions on how the item should be produced. E-Max ERP’s quality management system makes it easy to attach this drawing to the job/part master. The Quality Manager or a member of the Quality department usually has a responsibility to make sure it is the correct drawing. To save time and avoid disruption, E-Max ERP contains an approval system which allows an authorised user to check and approve that document.
Because E-Max ERP provides the user with the ability to view an attachment to a job/part from any area of our system, it allows any authorised user to double check drawings and specifications at any time in the production process.
Change control
Our QMS allows users to record changes and updates to any of the documents. This includes changes made by customers or by authorised internal staff. Any of these changes will be recorded through E-Max’s change control functionality, allowing users to initiate quality procedures for drawing revision changes and part revision changes. Every change to the drawings, plan or specification is also automatically linked to changes to the bill of materials and operations on a route.
As E-Max ERP is a fully integrated system, quality managers can easily review where parts are used and if this change may have any adverse implications on other parts.
Tests
Items for highly regulated industries, such as the oil or aerospace sectors, invariably have a number of tests. These tests may be done in process or when the item is complete to check its compliance to the requirements set by the customer. In E-Max ERP users can define these tests or checks at each operation. When the works order is raised the system produces a list of required tests. Test results can be recorded against individual tests and test certificates produced from these results. If third parties ie subcontractors, are involved, any test certificates provided by them can also be attached to the job.
E-Max’s quality management system also supports the creation of the final lists of documents (in PDF format) which accompany the final product to the customer. The system allows the Quality department to select which test certificates it requires to send to the customer.
Non Conformance
When things don’t go according to plan it is necessary to record what has happened and why. E-Max’s quality management system contains a full non conformance database which is integrated into our wider ERP system. Our software allows users to create work orders and route cards for rework and other quality related issues, such as machine repairs or material inspection.
E-Max’s non-conformance system has 8D process built in allowing you to perform root cause analysis, assign teams and allocate preventative actions and corrective actions as tasks to personnel, both internal and external to your organisation. Non-conformance reports can be produced at any time. With E-Max, companies can practice continuous improvement and discover the true cost of quality.
Traceability
As traceability becomes an increasing requirement throughout supply chains, it’s almost a necessity for manufacturers to have this functionality included within a quality management system. E-Max ERP automatically tracks every batch, serial/heat number, machine and operator involved throughout the production process. This data is easily accessed either through the job record or through individual batches. E-Max’s traceability reporting options make it simple to provide this information to the end customer.
E-Max can also record chemical and mechanical properties of material. These properties can be recorded against individual batches. In situations where a customer has a chemical and/or mechanical specification, users can easily identify items of stock that conform to the specification. The chemical and mechanical properties of any material used in a given job can also be included on the final certificate of conformity.
Calibration and Servicing
E-Max also offers the functionality to record any instruments, tools and gauges used by your company in an asset register. Every item held within the asset register can be tagged for calibration and servicing. Information such as last serviced, service due date and the results of these can be logged within E-Max’s quality management system.
When an item needs calibrated the system will remind the user by a report or via the system dashboard. Any problems identified during calibration and servicing can also be added to our QMS as an outstanding task.
A final bonus – as E-Max identifies these calibrated items as essentially stock items, users can buy and sell them and hence maintain a full assets register.
To improve your quality control management, call our team on 0808 109 2035 or message us today. Alternatively, you can request a free no obligation demo of E-Max ERP and take a look at our QMS. More information on our quality functionality can also be found here, complete with a case study on how GA Sliding Head have used our quality control system for continuous improvement.